Laying the foundation of an HVAC maintenance strategy: Examining the difference between centralized and decentralized models
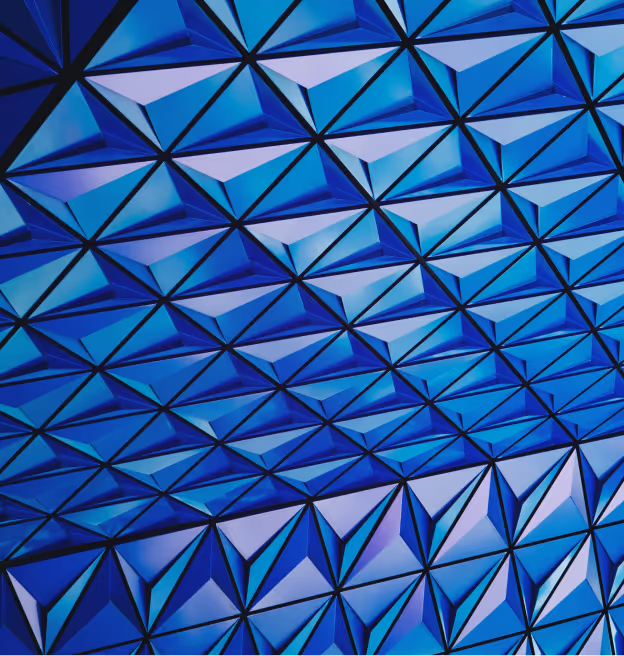
Deferring maintenance on HVAC equipment is not an option, but what should be done instead? Read to learn how centralizing HVAC maintenance services is the first step in building a robust HVAC strategy.
Delaying maintenance on critical HVAC equipment will only increase future facilities costs, but implementing the wrong type of maintenance strategy can have an impact on short- and long-term expenses while stagnating your overall facilities program.
When it comes to HVAC maintenance strategies, there are two basic approaches: decentralized or centralized. A decentralized model is a structure where each location is responsible for managing its own repairs. In a centralized model, maintenance and repair is handled through a single entity, either in-house or outsourced.
Building a robust HVAC maintenance strategy starts with choosing the right program that takes into account the entire system, long-term goals, and needs of the facilities department. First, it’s important to distinguish two types of reactive maintenance: emergency maintenance and corrective maintenance.
- Emergency maintenance is an activity that needs to be taken immediately to restore an asset’s operational capacity. Emergency maintenance is usually done to avoid any shutdowns, safety issues, or revenue loss.
- Corrective maintenance is fixing an asset that needs repairs but has yet to escalate into a failure. This type of maintenance is done to restore the asset to its optimal condition.
Even though this might seem like preventative maintenance, it is different because there is something that is causing the asset to need repair; it just hasn’t gone to complete failure—yet.
Decentralized vs. centralized
The benefit of a decentralized HVAC maintenance model is that each location gets control over how, when, and who does its maintenance. Each location is responsible for budgeting, scheduling, and assessing its assets.
However, these benefits are also the drawbacks of decentralized maintenance. Locations may defer maintenance issues to boost monthly P&L statements, overpay for services because the lack of competitive pricing, or not simply have the needed information to make critical decisions. In a centralized model, these issues are housed under one authority.
A centralized reactive maintenance strategy provides visibility and oversight on location spend, real-time data on services provided, and additional vendor support and scale when needed. Locations always plan for core services like plumbing, HVAC, and electrical work, but there are blind spots, too.
These are some of the benefits of centralized maintenance:
- Centralization and consistent tracking of asset information
- Consistent KPIs for better analysis and management
- Compliance with corporate standards across assets
- Baselines for benchmarking across assets
- Scalability of services across locations
From managing change at locations to getting corporate buy in, implementing a centralized maintenance strategy isn’t without its challenges. However, adopting a centralized strategy provides more streamlined operations, greater cost management, and increase vendor flexibility to address immediate maintenance needs.
First steps to a centralized strategy
Creating a centralized maintenance strategy for HVAC requires upfront planning. This includes identifying goals, understanding the current asset landscape, and determining which aspects would have the most immediate impact. When looking to implement a centralized maintenance strategy, make sure to address these areas before launching the program.
Identify mission-critical facility needs
These are the assets that the business cannot operate without.
- Mission-critical equipment includes rooftop HVAC units, components likes fans and blowers, and other mechanical controls
- These assets are responsible for moving air throughout a space while conditioning it, keeping spaces comfortable and safe for those inside
Create a reactive budget
Making repairs on a strictly as-needed basis can be very costly. Setting aside part of a budget to reactive maintenance will help to absorb any unplanned repairs in your budget. When doing this, take into consideration how different locations can be impacted in different ways. This includes geography, customer traffic, age of asset conditions, and weather. It’s possible to start creating a realistic budget by compiling this data and using it to provide reactive maintenance budgets by location.
Compounding data will provide greater insights into maintenance spend and performance.
Research dedicated technology platforms
Instead of having to track manually or through spreadsheets, using a dedicated technology platform can centralize all of this information and make it easy to use and digest. And over time, the compounding data will provide greater insights into maintenance spend and performance. The platform will allow you to validate every work order, track history notes, record asset information, and manage quality and performance.
Standardize work processes
Create a set of uniform invoice intake and processing requirements, record name of vendor performing work, and create a work order invoice form. This standardizes the work done across locations.
Determine if work can be bundled across locations
Fixing things as they are needed can slow down the process and cost more. If there are assets that need to be repaired, group the repairs together. This allows for more quickly scheduled maintenance, the resolution of issues in a single trip, and general a lower cost for repairs.
Identify not-to-exceed (NTE) thresholds
NTEs serve as an automatic threshold for work to be done. These thresholds are based on a historical analysis of acceptable dollar amount ranges for any given kind of work order.
If a work order exceeds the NTE threshold, vendors are required to contact a facilities decision maker to approve the additional costs. This provides more control and oversight of the maintenance program.
Options to manage operations
Outsourcing to a third-party to manage operations. Centralizing a reactive maintenance strategy provides greater insights into performance and spend while providing a deeper bench of vendors to performance services.
Moving to a centralized HVAC maintenance strategy provides more control over maintenance, better insight into spend, and a consistent approach to maintenance.
From improving first-time fix rates to making sure qualified vendors are always available, using a centralized maintenance model for HVAC repairs is the best first step in not deferring maintenance and setting up for a long-term HVAC maintenance strategy.
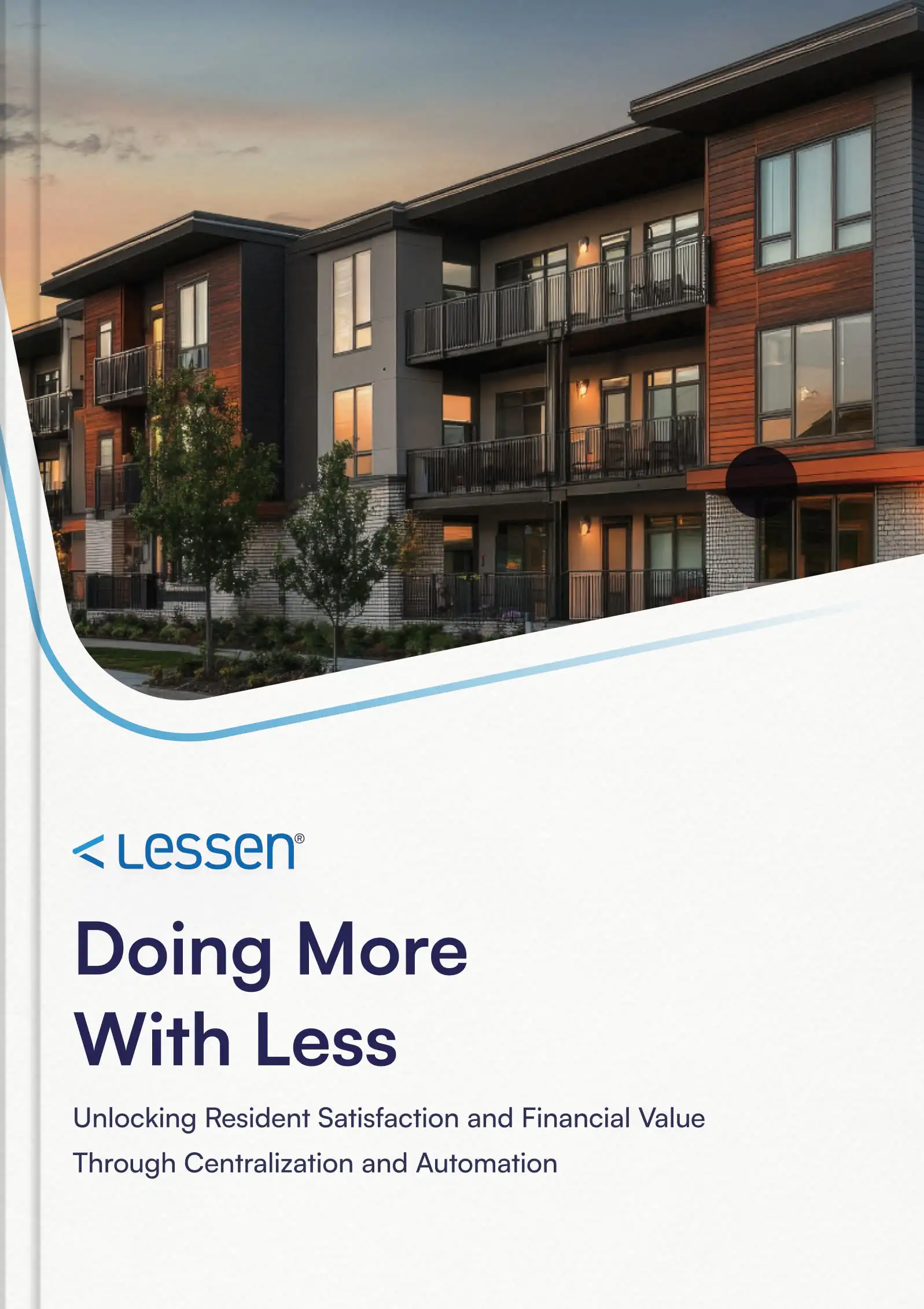
- This is my list