The true cost of deferring maintenance
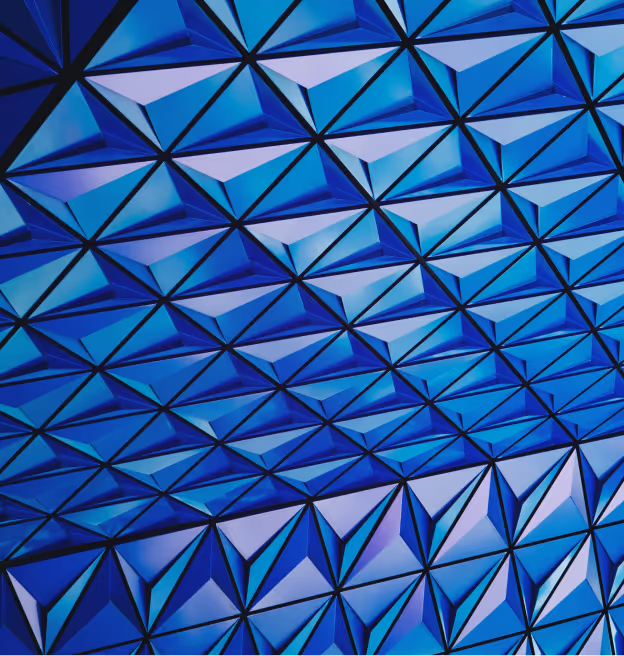
Balancing your budget by deferring needed maintenance isn’t the cost-saving move it seems. Read on to learn why deferring maintenance to future budgets can cost more in the long run.
In times of economic uncertainty—such as high inflation, weakening demand, and rising interest rates—companies often turn to budget cuts and operational efficiencies to protect their margins. And the first casualty is typically much-needed maintenance and equipment upgrades. While this might seem to be a reasonable approach, it can be counterproductive to long-term growth and business health and can ultimately negatively impact the core operations of a business.
Even in periods of economic stability, maintenance departments are often forced to operate with thin budgets, and facilities managers routinely find themselves under pressure from upper management to cut costs. Because upper management is usually removed from day-to-day operations, this desire to save money has created the flawed concept of deferring maintenance to future budgets. When faced with shrinking budgets, facilities managers need to make the tough decision as whether to delay general maintenance, system upgrades, or building repairs—or shelve them completely until dedicated funding becomes available.
The problem with this philosophy is that deferred maintenance only grows in scope—and cost—the longer it is postponed. Equipment is still subject to daily wear-and-tear where the needed repair can easily turn into a replacement. These areas become the most critical issues when deferring maintenance costs:
- Emergency replacement
- Reduced efficiency
- Shorter asset life
- Safety and health risks
Shifting budgets and timelines
Deferring maintenance shifts repairs and budgets from set timelines to when the asset needs to be emergency serviced or completely replaced. Instead of being able to plan for maintenance and CapEx, emergency repairs will eat into non-existent budgets, cause store or facility shutdowns, or at the least result in poor customer experiences.
Run to failure practices, which happens when no maintenance is done, can reduce lifespans from 20 years to as little as five to 10. For example, around 80 percent of HVAC issues are air flow related. As the equipment starts to degrade, it also becomes less efficient. HVAC systems that do not undergo regular maintenance see 20 percent more energy wastage than those that are served on a regular basis. By not changing filters or conducting regular cleanings, more stress will be placed on the system, causing HVAC units to overwork and potentially shorten their lifespans.
HVAC systems that do not undergo regular maintenance see 20 percent more energy wastage than those that are served on a regular basis.
Store shutdowns and unexpected costs are short-term financial aspects to deferring maintenance, but a larger, and even more potentially damaging element, is health and safety. Lack of maintenance on equipment in restaurants, especially grease and dirt buildup on HVAC elements, can introduce potentially hazardous elements into an environment. Not only will the repairs need to be addressed, but it could also result in potential fines. For buildings that defer maintenance, OSHA fines can range from $15,000 to $150,000 based on the severity.
So, what is leading to deferred maintenance and why are these decisions being made? It comes down to three factors:
- Maintenance teams are contending with fixed or declining budget
- No reliable reactive or preventative maintenance programs are in place
- No additional operational resources are made available to address long-standing issues
Long-term costs of deferring maintenance
However, over the long term, deferring maintenance will only result in exponentially higher costs, either through direct equipment replacement or through lack of efficiency. Simply changing HVAC filters every one to three months can reduce wasted energy by 5 to 10 percent and regular quality preventative maintenance can reduce commercial HVAC maintenance costs by 40 percent.
Deferring maintenance is a poor short-term strategy to deal with structural budget issues, but there are ways to get more money baked into monthly budgets to allow for equipment repairs. The goal is to build and present a case to those controlling the facilities and company budget:
- Assess your current facilities, including HVAC and other systems. Evaluate the condition of each asset and identify any deficiencies.
- Present evidence that supports the budgeting of immediate maintenance projects and projected future repairs.
- Develop a budget for equipment repair or replacement along with estimated timeframes for completion.
- Look forward to future budget constraints and savings through the implementation of a preventative maintenance program that reduces long-term costs.
Doing more with less, finding additional efficiencies, and macroeconomic pressures are always going to force facilities managers to look for ways to stretch budgets and get creative. While an attractive proposition, cutting maintenance budgets should be a last resort as it will have longer lasting impact on a facility’s operations, budget, and revenue than any temporary suspension of maintenance will save.
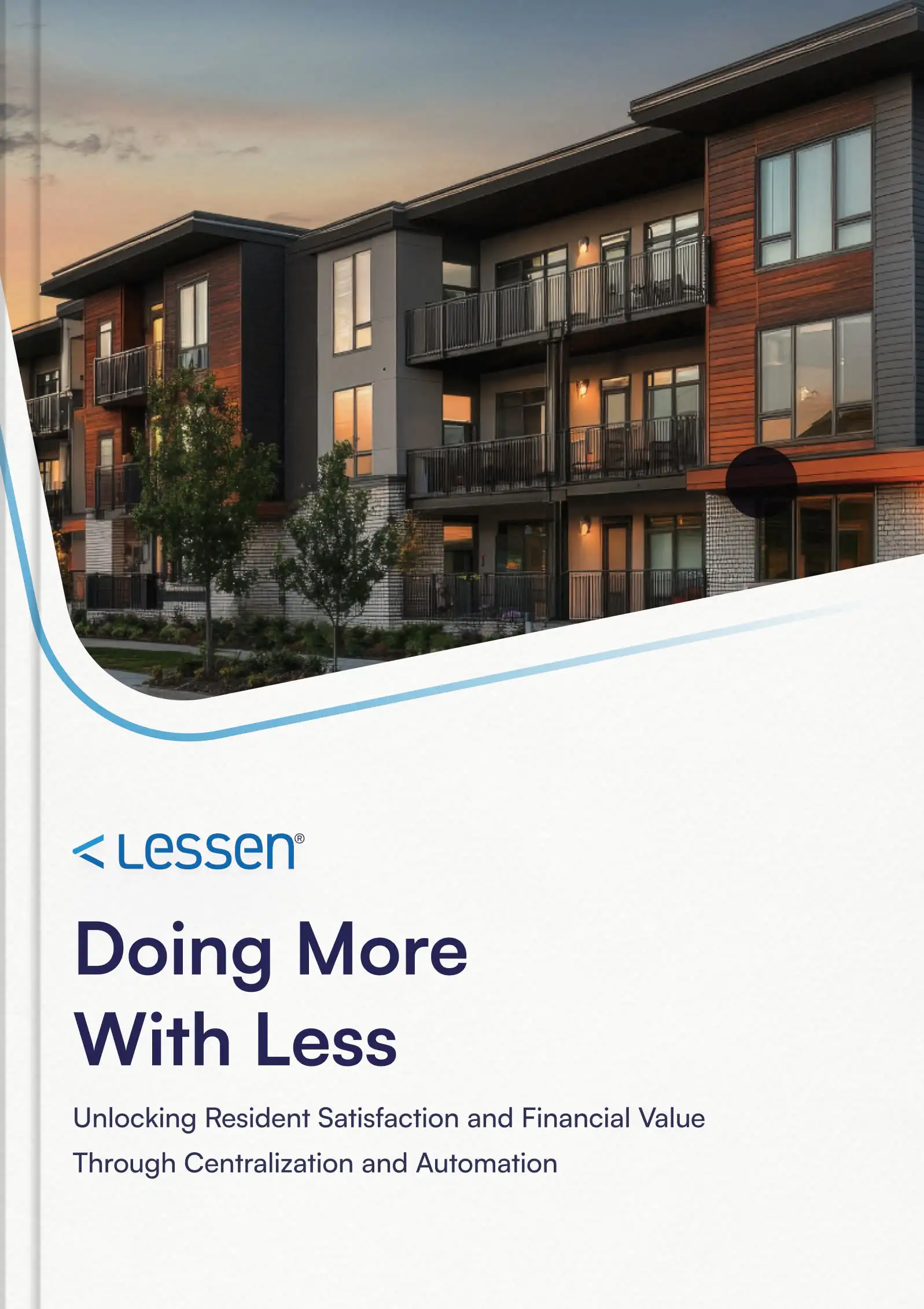
- This is my list