Winning customers when budgets are tight: how managing indirect costs can boost retail brand experiences and monthly budgets
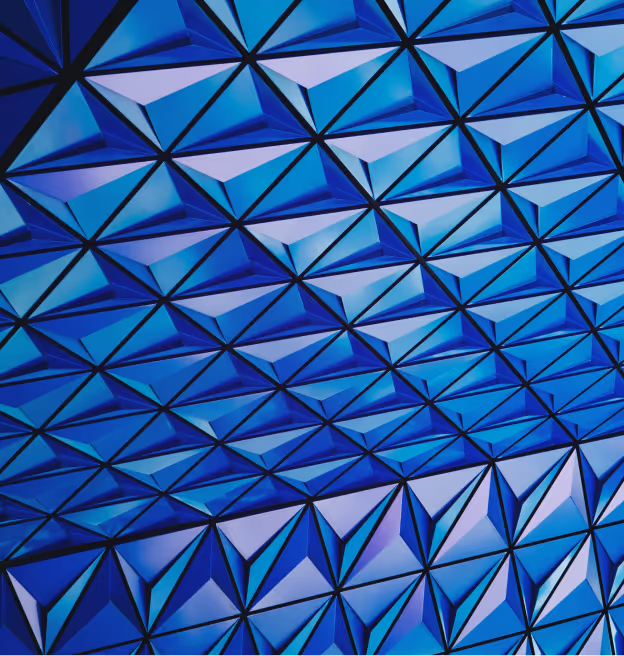
Coming out of the pandemic and with persistent supply chain and inflationary headwinds, consumers are increasingly budget conscious—especially when it comes to discretionary retail purchases. In general, retailers have two responses: passes on increased production costs to the consumer or maintain price while looking to cut elsewhere. However, it’s possible to hold direct product costs while at the same time lowering indirect costs and improving retail brand experiences.
Most shoppers gravitate toward retail, but in retail, value isn’t always about the price. Customers assign value to positive, memorable in-store experiences that are distinct and worthwhile. Part of this value comes for the look and feel of your location—the cleanliness of the bathrooms, the snow-free sidewalks, the comfortable environment. Focusing on these elements can improve retail brand experiences with customers, create a positive experience, and help customers to absorb some price inflation.
However, managing and maintaining retail facilities has also become more expensive because of persisting labor and equipment shortages. This has led to some difficult choices when it comes to maintaining and repairing equipment. Because of this, many retail operators will simply look for the lowest cost for equipment and repair. But this isn’t telling the whole story. In this discussion, we will define costs into two buckets for retail locations:
- Direct costs that include labor, food, supplies, tools, equipment, etc. that go directly into the cost of the end product.
- Indirect costs, which include the administrative overhead and other less tangible costs that impact the overall operation.
Indirect costs are often overlooked and are not applied back to direct ticket costs because they are less tangible than hourly rates and trip charges. This makes them harder to calculate for the total cost of ownership. However, without evaluating these indirect costs, you lose transparency to accurately calculate the financial impact on your business.
Below are a few of the indirect operational costs for facilities and explained how they impact your bottom line.
Emergency repairs
Unexpected breakdowns or failures of equipment or systems can result in unplanned expenses for repairs or replacements. These emergency repairs can quickly add up and strain the budget, especially if they occur frequently. They can also disrupt operations, leading to potential downtime and lost productivity, further impacting the budget.
Deferred maintenance costs
Delaying routine or preventive maintenance can result in increased costs in the long run. Equipment or systems that are not properly maintained can deteriorate faster, leading to more frequent breakdowns or failures. This can result in higher repair or replacement costs and increased downtime, negatively impacting the budget.
Operational Disruption
Most retail environments have critical assets or components of their day-to-day operations that impact their ability to generate revenue. Should this asset or component of their building not be operational, it will result in potential lost sales or even damage retail brand experiences. The down time of the asset or component of their building should be accounted for within the cost to repair.
For example, should the outlets at a store stop working, this will potentially limit or even stop a service altogether. This will directly result in a negative customer experience as well as impact total sales revenue. The estimated lost sales per hour should be applied back to the cost of the repair. Applying lost sales to the total ticket cost will not only enable an organization to more accurately measure the total cost of a service, but also the effectiveness of the current program.
Compliance costs
Compliance with regulations, codes, and standards related to facility maintenance, such as safety regulations or environmental requirements, can result in additional costs. These costs may include inspections, certifications, permits, or fines for non-compliance. Failure to comply with these regulations can result in legal liabilities and financial penalties, negatively impacting the budget.
Realizing true facilities maintenance costs
Total cost of ownership analysis provides facility maintenance teams and executives with a more accurate picture when measuring the effectiveness of their program. When looking at the total cost of ownership from a facilities maintenance perspective, it is essential to know and understand the indirect operational costs that affect your business.
Getting the most out of your facility management program will help to ensure that your locations maintain the comfort and cleanliness the customers expect in an increasingly competitive landscape. To ensure they keep receiving excellent service, make sure to look at the total cost of your facilities management solution and not just the cheapest initial quote.
A well-functioning maintenance strategy is essential to the success of any modern-day facilities portfolio. To make sure your facilities maintenance strategy is meeting your needs, request a demo to learn more about how our programs can help you.
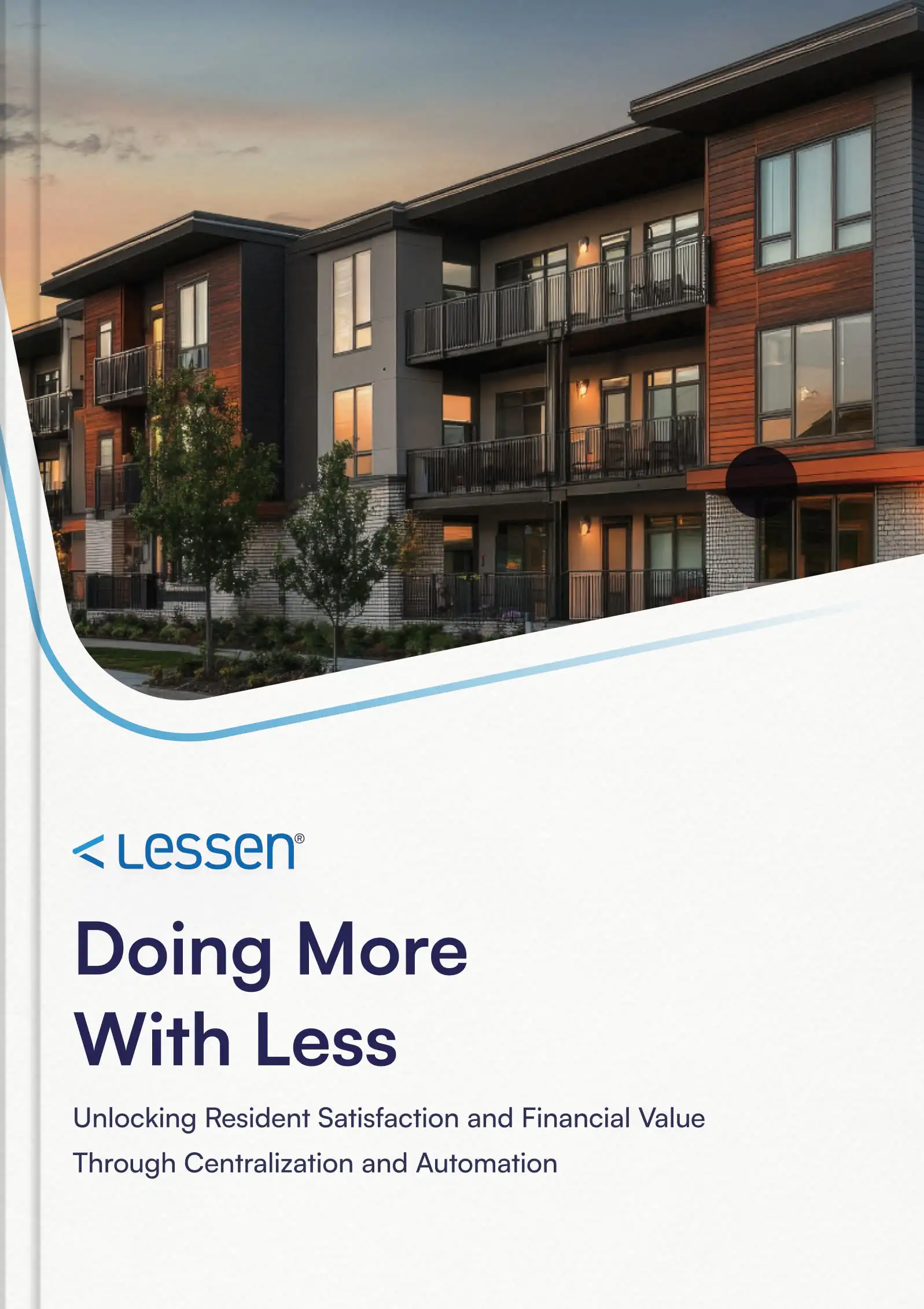
- This is my list