Telecom right to repair can strain locations: four preventative maintenance strategies that can help
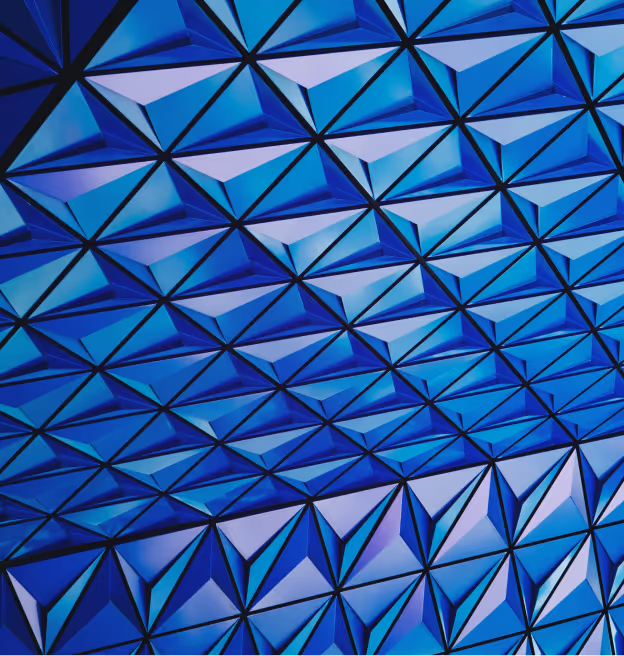
In the telecom industry, there has been steady interest in the right-to-repair movement where owners are able to repair or have the phones repaired. Over 40% of people say that reparability is very important when buying a mobile device, and lawmakers in nearly 20 states are considering right-to-repair bills.
With on-going labor shortages adding to many retailers’ challenges, providing additional tech support for phone repair is one more budget expense. And one of the first budget casualties has one of the most outsized impacts on customer satisfaction: facilities maintenance.
Facilities maintenance affects employee productivity and the overall customer experience. No matter how exciting the product or enticing the deal, a location with dirty, broken, and uncomfortable environments detracts from the overall buying atmosphere. Beyond its direct, visible benefits, preventive maintenance contributes to soft benefits, such as customer perception and satisfaction, carry weight, according to FacilitiesNet.
The hard-dollar bottom line of preventive maintenance is this: It has a demonstrable positive impact on the budget. We look at the following four areas where preventative maintenance can lead to a healthier budget to absorb rising costs.
Reduced Repair Costs
Having a poorly managed maintenance schedule can result for as much as 40% of an operational budget—with most of this coming from costly repairs due to inadequate preventative maintenance. Unfortunately, many businesses put preventative maintenance low on the priority list, which eventually will cost two, three, or even five times as much when it is time for repairs.
Preventative maintenance reduces repair costs because it catches smaller issues early. Left unchecked, small material defects on-site can turn into major, cross-departmental expenses. Creating and implementing a preventative maintenance schedule ensures that everything from scheduled inspections to routine cleanings mitigate potential interruptions due to mechanical system malfunctions. As an example, scheduled, routine maintenance for flooring can removes grit that builds up, heads off surface corrosion, and in the case of plumbing, can identify and fix leaks mitigating potential floods and damage to assets and merchandise.
Lower business operation costs
The U.S. Department of Energy recommends monthly HVAC maintenance to maximize efficiency and lower operating costs. In reality, most commercial businesses are doing this at most twice a year. With 80% of HVAC issues related to air flow, something as simple as a dirty filter adds stress to the intake system and increases energy consumption, ballooning operational costs and eventually leading to costly repairs due to reduced asset lifespan.
Few assets are durable and resilient enough to perform like new for their entire lifespan without preventative maintenance. Whether its HVAC, mechanical systems, or plumbing, poor performance adds up to higher business operating costs. Preventative maintenance programs ensure that equipment is serviced regularly and according to actual usage and local environments.
Preservation of big-ticket investments
Asset management and capital expenditures can lead to higher operation costs incurred by a business. Roofs, flooring, and HAVC systems are expensive to replace and require multi-year CapEx plans. Spot repairs and supplemental solutions may extend the useable lifespan of some of these assets, but it only delays the inevitable of complete replacement. Add in long lead times and the costs can go exponentially higher.
Moreover, when some systems give way to defects there can be a ripple effect on other assets, other which can compound the repair and replacement cycle. As an example, according to the Journal of Architectural Engineering, a failing, leaking roof compromises the whole building envelope, potentially creating both structural and equipment damage. Preventative maintenance protects it.
Effective implementation of preventative maintenance program can ensure and sometimes extend an asset’s manufacturer-determined lifespan while reducing strain on reliant systems. Creating a strategic CapEx plan to replace equipment at the end of its lifespan versus when it prematurely fails introduces budget predictability in the short term but also over the next five years for planned upgrades. Through a CapEx plan, businesses can budget and reduce the procurement costs through leveraged buying.
Better brand image and customer relations
Perhaps one of the greatest advantages of a maintenance program is reduced downtime. In a restaurant, for example, preventative maintenance can keep equipment working as planned which results in keeping the food and business running. In a retail store, maintenance heads off electrical malfunctions before they interfere with business. Consider that 95% of shoppers say that unclean restrooms and unpleasant odors influence their shopping decisions along with dirty floors, spills or stains, and other factors.
A reactive maintenance approach will contain surprises because you won’t know what to fix until it breaks. This can wreak havoc with budgets. Preventative maintenance puts you in control of your budget, which leads to better building integrity, performance, and brand reputation.
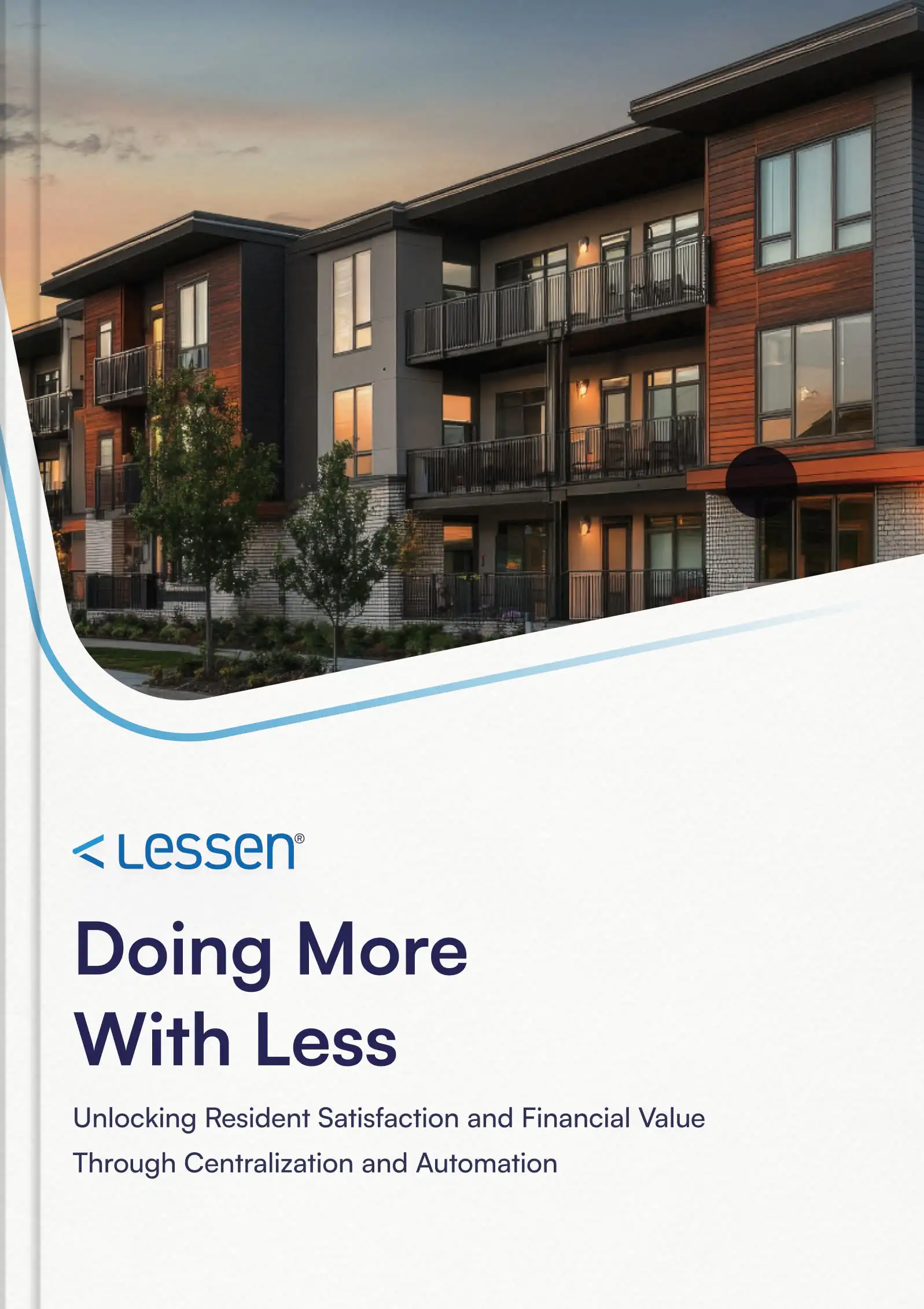
- This is my list