SMS Assist reports: State of snow and ice management 2023
-min.avif)
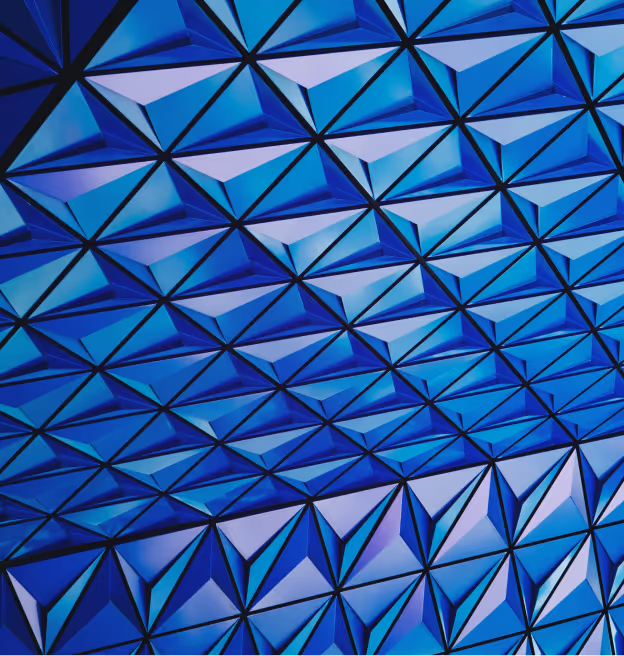
After more than 168,000 snow and ice management work orders, we’re looking back at this past year’s winter season to learn more about how everything from shifting weather patterns to higher costs are impacting the industry and what to expect next year.
In the face of unprecedented challenges posed by rapidly shifting weather patterns and evolving economic landscapes, managing snow and ice removal has become increasingly more challenging. This analysis looks to shed light on the critical connections between weather, inflation, and labor. This will provide decision-makers with insights to navigate this rapidly changing landscape and how to better prepare for the future.
About the data
The data used for this analysis comes from work done by SMS Assist’s vendor base. The included dates are from October 1, 2022, to April 30, 2023, which is the typical snow and ice season for the United States not including Alaska and Hawaii. This is the scope of work used in the analysis:
- 1,483 vendors
- 168,000 work orders
- 7,377 sites
- 47 states
Duality in snow across the U.S.
To understand the data, it is necessary to understand what happened during this past winter season. Like many industries, snow and ice management companies are grappling with the consequences of shifting weather patterns driven by climate change. Unpredictable storms, extreme temperature fluctuations, and irregular snowfall pose significant challenges. This year was no different. The western half of the U.S. saw nearly unprecedented levels of snow and cold. However, the eastern half of the U.S. was warmer with more precipitation falling as rain instead of snow.
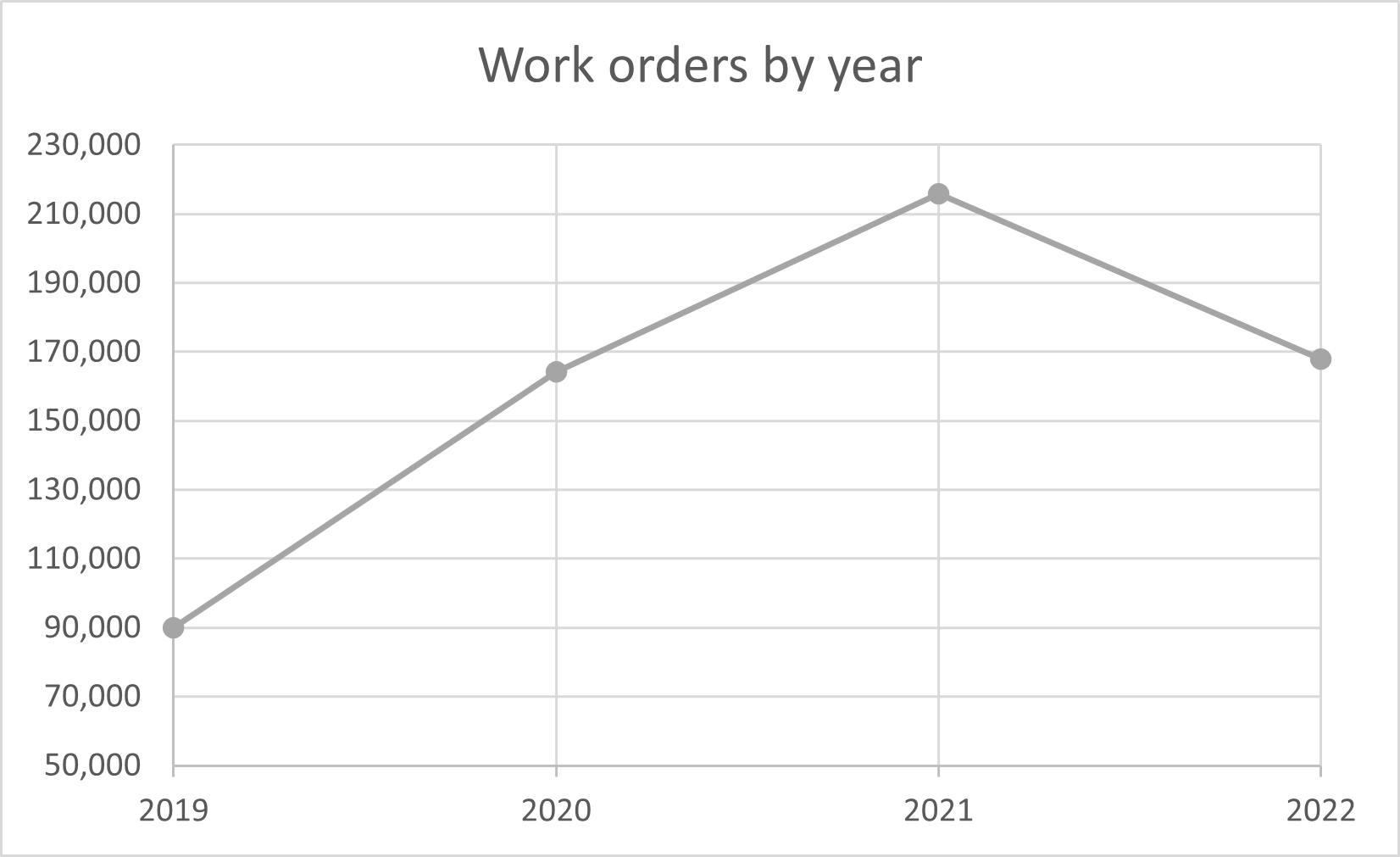
Even though the cost per work order has steadily increased, the lack of snow in the eastern part of the U.S. reduced the number of work orders year over year by nearly 25 percent and the total number of sites by nearly 16 percent.
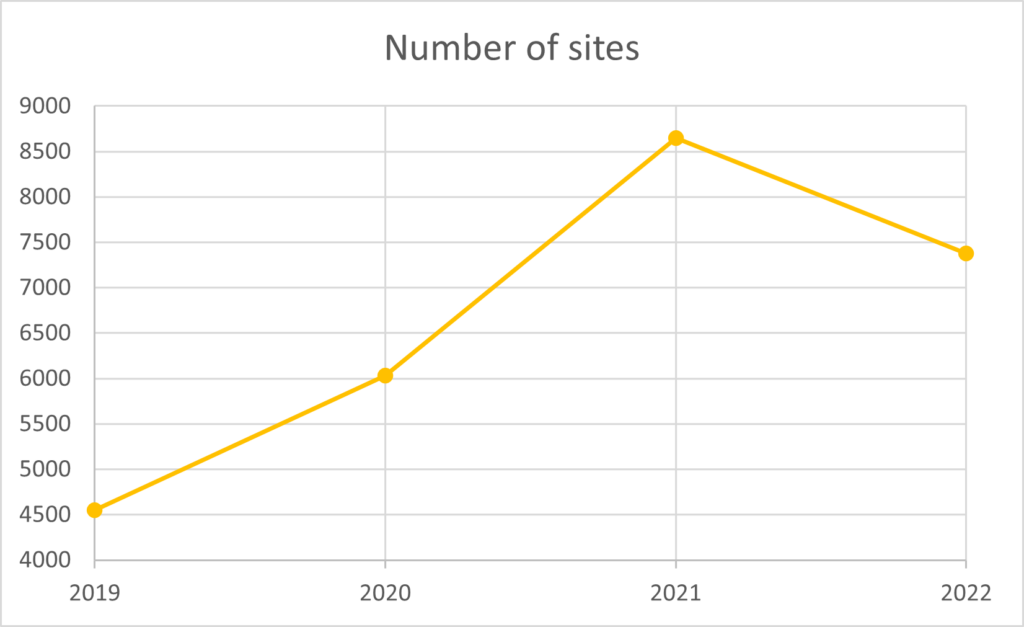
When planning for next year’s snow season, keep these considerations in mind:
- Increased frequency and intensity of storms: Many regions are experiencing more frequent and intense snow and ice events, necessitating more resources, equipment, and labor to address the heightened demands.
- Unpredictability: Erratic weather patterns make it difficult to anticipate when and where snow or ice events will occur. This unpredictability affects planning, resource allocation, and operational efficiency.
- Changing snowfall patterns: Some areas may experience altered snowfall patterns, such as heavier or lighter snowfall, impacting the required equipment, de-icing methods, and overall operational strategies.
Rising costs and the impact of inflation
For this past year, the average cost per work order rose to $138. That’s just over 4 percent higher than the previous year and over 17 percent higher since the 2019 season.
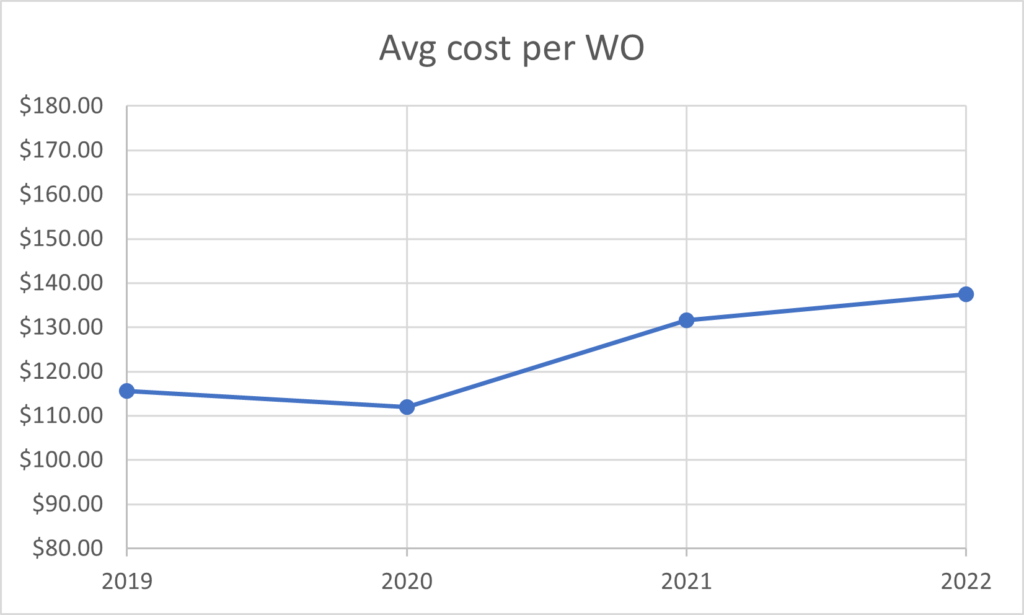
Looking at long-term trends, costs fell during the height of the pandemic when many locations where closed. However, since reopening, overall average cost per work order has risen with the jump from 2020 to 2021 increasing by over 16 percent. This trend reflects the broader economy. Even though inflation is cooling compared to 2022 levels, it is still above historical levels, and for providers and property owners this is leading to additional cost management challenges.
As companies strive to deliver exceptional services while maintaining profitability, understanding the driving forces behind inflation and implementing effective cost management strategies becomes imperative. When creating budgets for next year, keep these factors in mind.
- Increased equipment and material costs: Snowplows, de-icing agents, and other necessary equipment and supplies have become more expensive, straining budgets and impacting the overall cost of operations.
- Fuel and energy expenses: Even though energy prices have been lower recently, they are historically volatile. Rising fuel and energy costs can directly affect snow and ice management companies, as they heavily rely on vehicles and machinery for clearing operations.
- Insurance premiums: The impact of snow and ice on insurance hasn’t been seen as strongly as that with hurricanes and wildfires in Florida and California respectively. However, the insurance costs associated with snow and ice management services have risen due to the potential liability risks involved, further adding to operational expenses.
Managing labor shortages
Like many other parts of the economy, the snow and ice management industry faces ongoing labor shortages. However, this isn’t evenly distributed due to shifting weather patterns. In the East where snow has typically been more frequent, there are more historical service providers than in other places, such as Texas, that have not historically seen snow and ice events until recently. This is leading to labor shortages in certain parts of the U.S. with excess capacity in others. Recent data show a slight leveling off of vendors available from 2021 to 2022; however, the number of vendors per site has remained steady due to the unpredictable nature of winter storms. The average cost per site was also lower in 2022 compared to 2021, resulting in a nearly 5 percent reduction in total spending by site for the season, but this remains elevated compared to the 2020 and 2019 seasons.
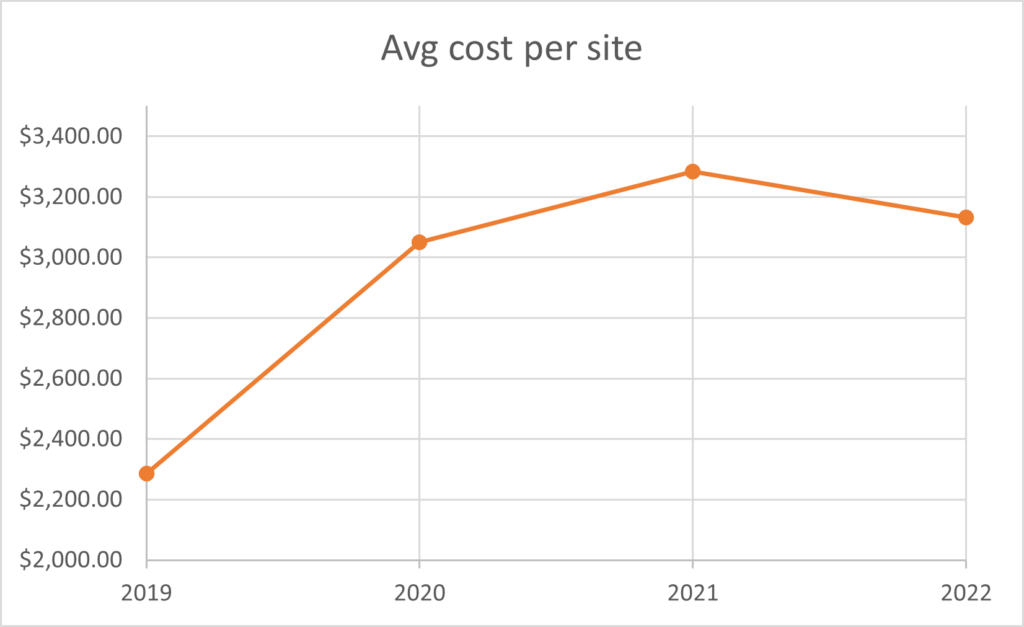
Cost management strategies for facility managers
Adapting to shifting weather patterns, managing rising costs due to inflation, and addressing labor shortages are critical challenges faced by commercial companies with distributed portfolios. To overcome these hurdles, facility managers can consider the following various short- and long-term strategies.
Efficient resource allocation: Optimizing resource allocation is crucial to cost management. This involves analyzing operational processes, identifying areas for improvement, and streamlining workflows to reduce waste, enhance productivity, and control expenses.
Technology integration: Embracing technology solutions, such as optimization software, real-time reporting systems, and automatic triggering, can enhance operational efficiency. These tools enable companies to make data-driven decisions, optimize resource utilization, and reduce costs.
Strategic partnerships: Collaborating with providers can help businesses, especially those with multiple sites, to secure favorable pricing, vendor coverage, and ensured service. Building strong partnerships within the industry can contribute to long-term cost savings.
Long-term contracting: Establishing long-term contracts with providers allows companies to stabilize budgets and forecast future costs more accurately. It also provides an opportunity for strategic planning and cost optimization over an extended period that goes beyond the winter season.
By embracing these strategies and staying agile in the face of changing circumstances, companies can ensure that they are able to provide their services and ensure the safety and mobility of their employees and customers even in the face of shifting weather patterns and industry challenges.
-min.avif)
- This is my list