Fine-tuning work order priority levels saved this retailer 5.3% of its annual facilities spend
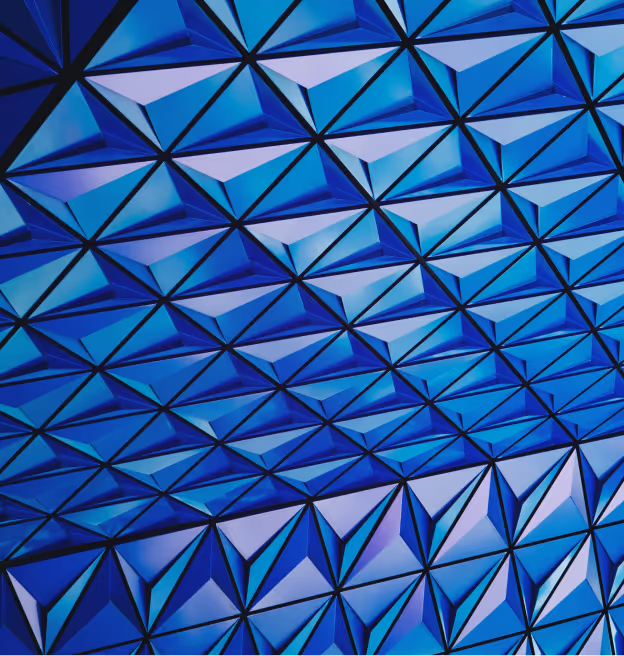
Work order priority levels can strongly influence performance and cost in a maintenance portfolio.
The challenge
Working with another facilities management provider, a leading pet retailer suffered high costs and poor performance throughout its portfolio. It was time to find a new solution.
The retailer turned to SMS Assist. In the Discovery phase of the customer onboarding process, SMS Assist performed a wide-ranging data collection and analysis effort to understand the customer’s portfolio.
As part of this effort, the Business Analytics and Operations teams compared the retailer’s historical work order data against their own models and discovered a trend—even across different trades, geographic locations, and service providers, work order priority levels were unusually high. More digging uncovered that 75 percent of the retailer’s work was categorized as urgent. Was all of this work really urgent?
The solution
The Operations and Business Analytics teams partnered with the retailer to align future work with SMS Assist’s priority level adjustment models. Here’s how it works: SMS Assist work order priority levels are charted on a four-point scale, from highest (1) to lowest priority (4). Every work order is given a priority level that influences many other variables within our system, including:
- How our alignment models assign work to our network of Affiliates
- How Operations teams manually queue and dispatch work
- How SMS Assist’s trade specialists—subject matter experts with years of field experience—suggest repair, replacement, or deferred maintenance
- How service billing is calculated
Even the slightest change to priority levels can have a positive long-term effect on the way service is dispatched, performed, billed, and recorded as data. For this retailer, those realignments included:
Moving 18 percent of all work orders from Priority 1 to Priority 2
For this retailer, that meant reprioritizing broken refrigerators, leaking toilets, door handle repairs, and critical parts back orders.
Moving 31 percent of all work orders from Priority 2 to Priority 3 or 4.
For this retailer, that meant reprioritizing damaged ductwork, air filter orders, and non-essential parts back orders.
The result
5.3% in annual savings by adjusting priority levels
87% average first-time fix rate within the first year
Cleaner data sets over the long term, for even better performance and even more savings
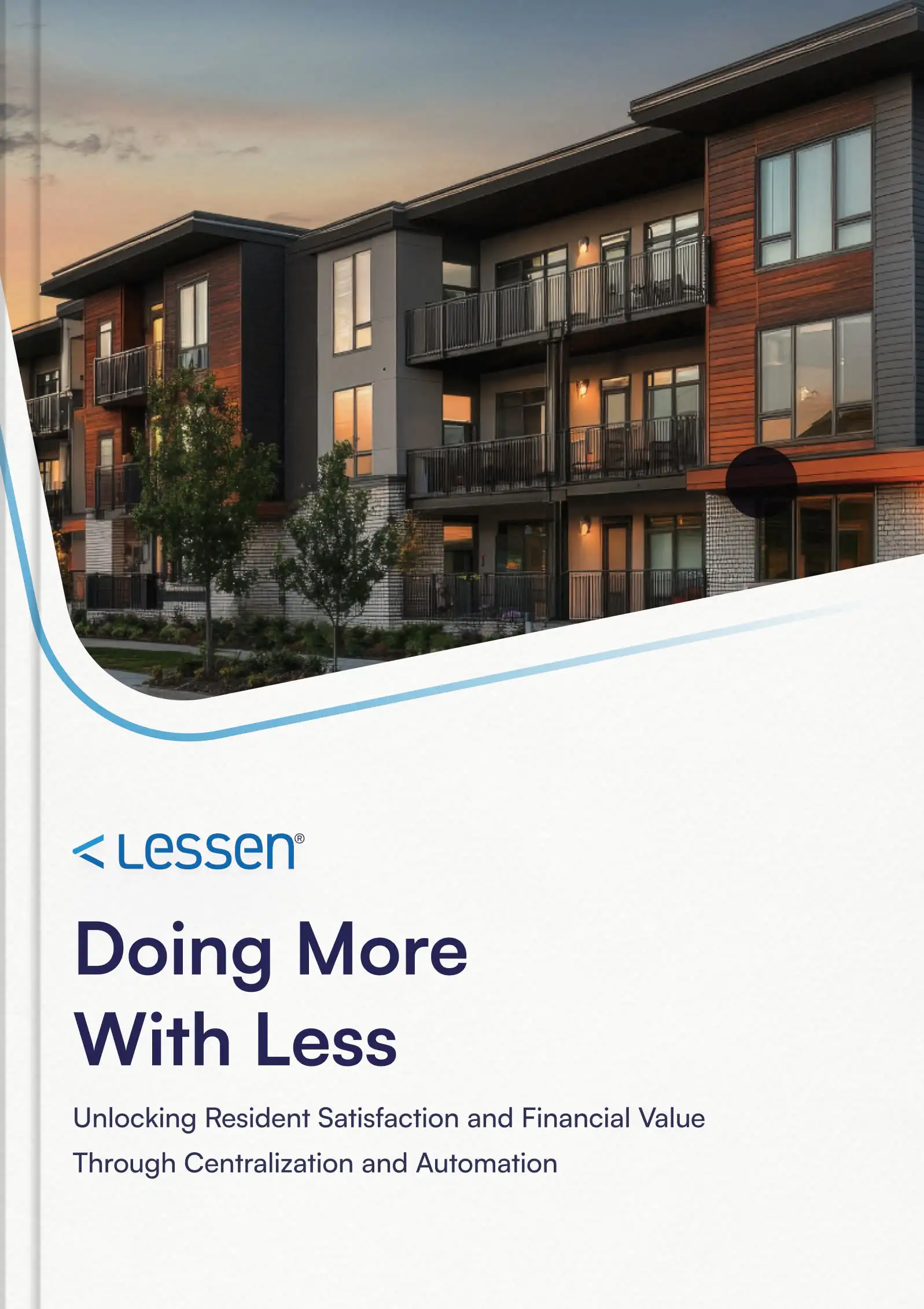
- This is my list