The Difference Between Preventative and Predictive Maintenance for Commercial HVAC Systems
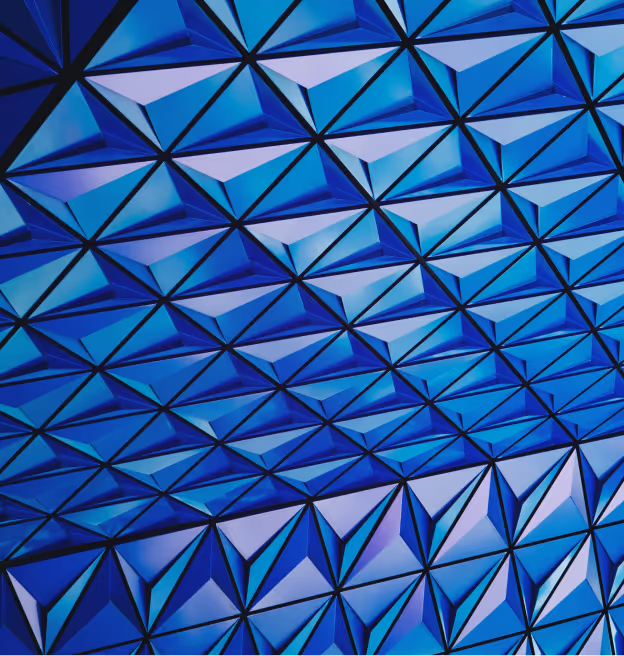
The efficient operation of heating, ventilation, and air conditioning (HVAC) systems is crucial for maintaining a comfortable and healthy environment in any building. However, HVAC systems are complex and can be prone to breakdowns and inefficiencies, which can lead to costly repairs and downtime.
Preventative and planned maintenance strategies prioritize the regular upkeep of HVAC systems to prevent failures and ensure optimal performance. The key is understanding the difference between each.
Preventative maintenance
Preventative maintenance for commercial HVAC systems involves conducting regular inspections, cleanings, and servicing of equipment to prevent potential issues and ensure efficient and reliable operations. Scheduling routine maintenance checks ensures the reliability and longevity of HVAC assets and avoids many of the most expensive and disruptive kinds of reactive repair needs that arise from ordinary long-term asset function.
Benefits of preventative HVAC maintenance program
Preventative maintenance addresses problems before they become critical fixes. These are key reasons why it’s important to perform regular maintenance on commercial HVAC systems:
- Energy efficiency. Regular maintenance helps to optimize HVAC performance, ensuring assets operate at their highest efficiency. Ensuring free airflow throughout the system with clean coils, filters, and well-calibrated controls, can reduce energy consumption, resulting in lower utility bills and greater cost savings.
- Reliability. Preventative maintenance helps to identify and address minor issues before they escalate into major problems that can lead to unexpected system breakdowns. This reduces the risk of costly emergency repairs and ensures that HVAC systems are operating when they are needed the most.
- Extended equipment lifespan. Commercial HVAC systems are significant investments, especially across a distributed portfolio that might extend into multiple geographical regions. Keeping equipment clean and well-calibrated can minimize wear and tear, keep air flowing freely throughout the system, and reduce the need for premature, and costly, replacements.
- Indoor air quality. Poorly functioning commercial HVAC systems can cause an imbalance in air pressure and result in particles being redistributed throughout a location instead of being circulated through the HVAC system. Clean and properly functioning HVAC systems play a crucial role in maintaining indoor air quality in commercial buildings. Cleaning and changing filters can help to reduce dust, dirt, food, and allergens in the air, creating a healthier and more comfortable environment for employees and guests.
- Compliance with regulations. Commercial buildings are subject to numerous and various regulations and codes such as energy consumption, emissions, and safety. Regular maintenance ensures that HVAC systems are complying with local rules and helps to avoid any fines or penalties.
Establishing a successful preventative maintenance strategy
Commercial HVAC systems are complex and consist of various components such as furnaces, boilers, air handlers, compressors, fans, pumps, and controls—all of which require regular maintenance to operate at peak performance.
Preventative HVAC maintenance comes in two basic categories: major and minor.
Major HVAC preventative maintenance should be performed every six to 12 months, and covers essential asset components like coils, bands, moving parts, motors, and sensors.
- Moving parts: Bearings, belts, and other moving components should be lubricated or replaced if they show signs of considerable wear and tear.
- Electrical components: Electrical problems related to connectors, fuses, wires, and circuits should be ruled out during your major PM inspections. Shortages and other imbalances can cause sudden failures and potentially drive up your energy expenditure.
- System calibration: Sensors naturally become less accurate over time and should be calibrated or replaced outright to ensure optimal performance.
Minor HVAC preventative maintenance should be performed more frequently to ensure the optimal function and cleanliness of more temporary, easily replaced asset features like filters, covers, and grill inserts.
With a regular PM schedule and a thorough checklist, you can identify potential sources of HVAC system interruption and damage well before any issues present the most serious signs of concern.
Key takeaways:
- A preventative maintenance schedule can help you avoid many reactive repair needs
- A major PM schedule and a minor PM schedule will help you prioritize important repair tasks
- Preventative HVAC maintenance is inexpensive when compared with reactive maintenance requests, and improves performance and spend over the long term
Predictive maintenance
Predictive maintenance is the most advanced form of commercial HVAC asset maintenance, and in an advanced HVAC maintenance program, it should be primary focus of attention. This type of maintenance strategy collects accurate and consistent data on your HVAC asset portfolio including repair history, energy usage, and performance to predict and prevent potential equipment failures before they occur. This data is analyzed to detect patterns, trends, and anomalies that may indicate impending failures or degradation of performance.
Predictive maintenance for commercial HVAC systems can help facility managers to make informed decisions about maintenance, resources, and system performance. Some common tactics used in predictive maintenance for commercial HVAC systems include:
- Condition monitoring: Continuous monitoring of system parameters, such as temperature, pressure, and energy consumption, to detect abnormal behavior or trends that may indicate potential issues.
- Fault detection and diagnostics: Using algorithms and machine learning techniques to analyze data and identify patterns that indicate equipment faults or performance degradation.
- Predictive analytics: Leveraging historical data, statistical models, and machine learning algorithms to predict future failures or performance issues based on patterns and trends observed in the data.
- Remote monitoring: Using cloud-based platforms and Internet of Things technologies to remotely monitor and manage HVAC systems in real-time, allowing for early detection of anomalies and proactive maintenance actions.
- Data integration: Collecting and integrating data from various sources, such as sensors, building management systems, and maintenance records, to gain a holistic view of the HVAC system's health and performance.
- Maintenance planning and scheduling: Using predictive insights to optimize maintenance planning and scheduling, ensuring that maintenance activities are performed at the most opportune times to minimize disruption and downtime.
Benefits of a predictive HVAC maintenance program
One of the key benefits of predictive HVAC asset maintenance is the reduction in direct maintenance costs. Reactive maintenance, which involves fixing equipment only after it breaks down, can be costly due to emergency repairs, replacement parts, and lost productivity and revenue. Predictive maintenance, on the other hand, can identify potential equipment failures before they occur, allowing for proactive and preventative repairs that are less expensive and less disruptive to your operations.
Another benefit of predictive HVAC asset maintenance is increased equipment reliability and uptime. By using data analytics to monitor and predict equipment performance, companies can identify potential equipment failures before they occur and schedule maintenance proactively. This approach can help to reduce downtime and ensure that critical equipment is available when needed.
Additionally, predictive HVAC asset maintenance can improve energy efficiency and reduce energy costs. Energy usage accounts for roughly 40-50% of any organization’s total facilities spend. By identifying equipment issues that can cause energy waste, your organization can take proactive steps to address these issues and improve equipment performance—resulting in lower energy bills and lower total impact to the environment, a critical consideration for organizations looking to bolster their sustainability efforts.
Establishing a successful predictive HVAC maintenance program
Establishing your predictive HVAC maintenance program requires some up-front investment of time, effort, and resources. Even so, you can expect this investment to deliver multiples of that in value over the life of your program. Every HVAC asset portfolio is unique, but the below recommendations will help you get started as you strategize and plan your program.
Make a comprehensive HVAC asset inventory
Start by creating an index of the HVAC assets currently in use across your business. Record the make, model, serial number, year of manufacture, and any other identifying information that might be useful to a technician not familiar with your specific asset inventory.
Determine performance data to be collected
Predictive maintenance is only as powerful as the type and amount of data you’re using to make predictions. Operating temperatures, motor currents, pressures, flow rates, energy consumption, run times, and even weather data provide an important initial baseline. In addition to these ongoing records, you should keep a general repair and maintenance history for each of your HVAC assets, so that repair history information can be judged against operating data and leveraged for more accurate predictions.
Invest in a data analytics technology platform
To organize, process, and analyze the data you’re collecting with your predictive program, a data analytics platform is necessary. Invest in a technology platform that can easily handle a large volume of data, provides automation and machine learning capabilities, and can provide real time alerts when any concerns arise.
Key takeaways:
- Data-driven, predictive HVAC maintenance promises the best outcomes for your business.
- Predictive HVAC maintenance requires an initial investment, but it’s worth it.
- Make tailored adjustments over time to ensure optimal asset performance and spend.
Developing a predictive HVAC asset maintenance program is complex, but you don’t have to do it alone. To achieve the greatest benefit up front, consider working with an expert partner—one that provides consultation from dedicated subject matter experts, advanced technology, and access to a network of qualified, vetted HVAC maintenance vendors. Contact Lessen to learn more.
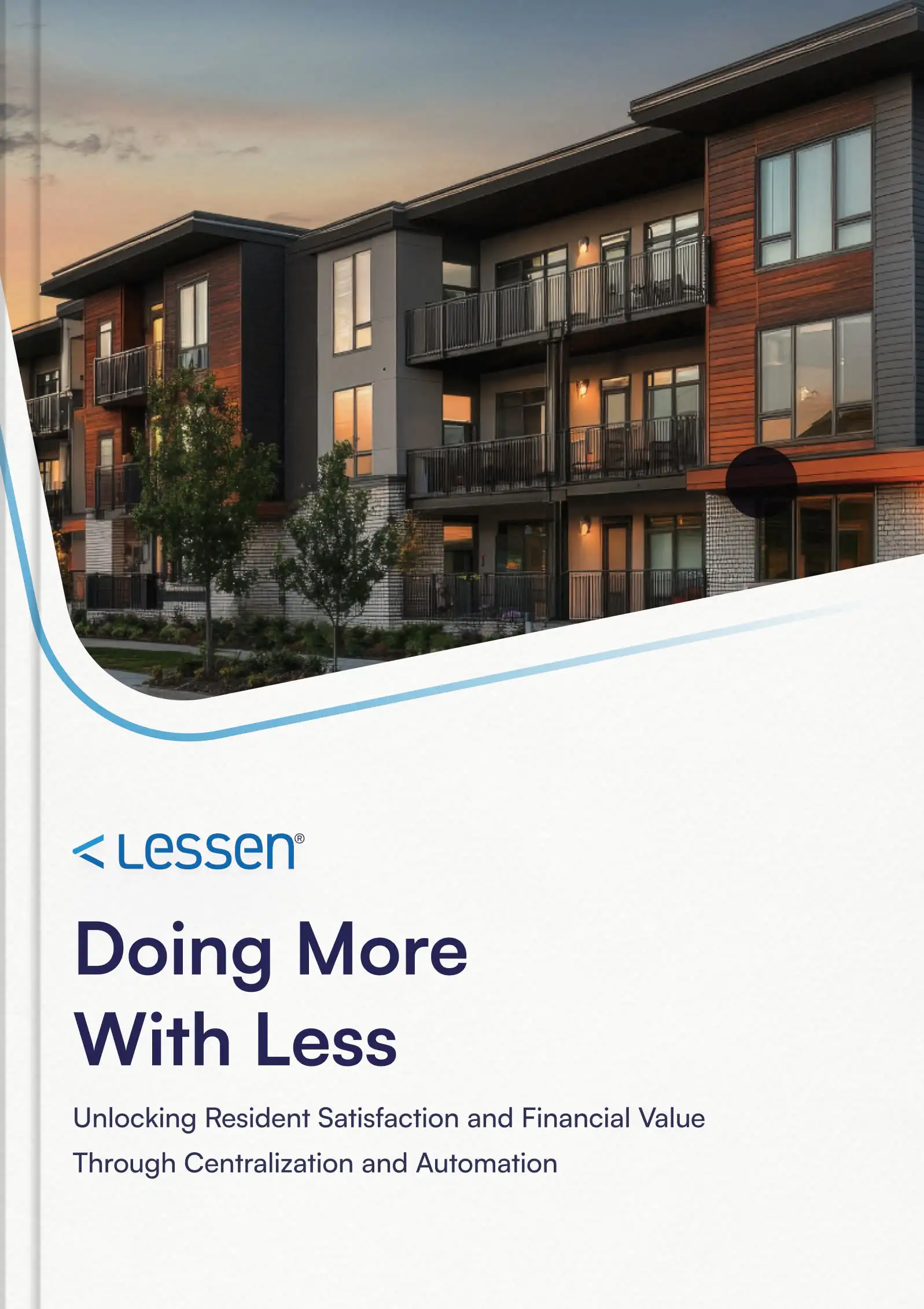
- This is my list