How to avoid buyer's remorse during snow and ice season
.avif)
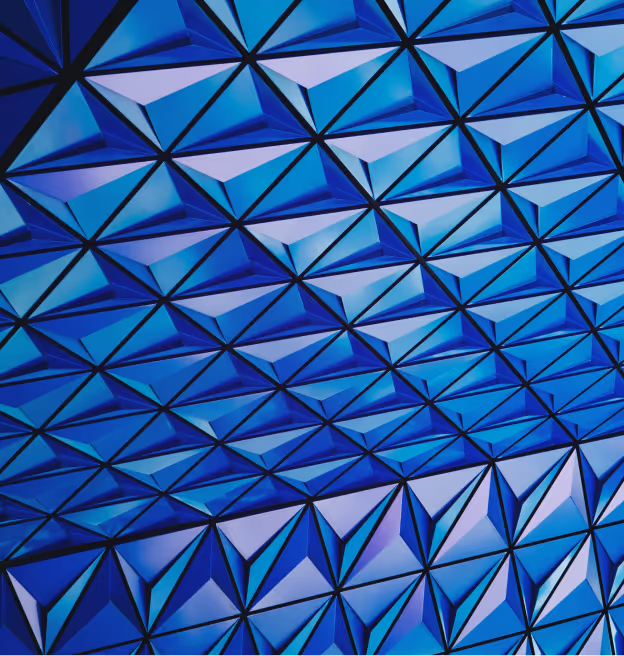
We all know the sense of regret in the pit of our stomachs after making a shortsighted purchase. Facility executives who are the decision-makers behind snow removal programs can also identify with buyer’s remorse when a snow season ends and they have to pay the operational and financial costs for inadequate snow removal services.
Facility executives should change the way they select their snow removal plan if they want to prevent further remorse and achieve new results during snow and ice season. Here are four ways facilities executives can avoid regretting next snow season’s cost:
1. Learn From Your Mistakes
When unpredictable weather occurs, upkeep and profit may suffer, resulting in damage to the brand’s reputation. Companies can lose sight of a planned budget during the snow season because they want to reduce hassles at their facilities. Tacking on additional services to a predetermined scope of work to handle the weather can throw budgets off track. When this occurs, facility executives should take action, reevaluate their snow removal plan and make decisions that offer their facilities the most value over time.
For example, proactive de-icing services can soften the blow when snow events come around. Eliminating the stress associated with risk management allows the facilities’ staff to focus on the customer experience. Planning proactive de-icing services with a snow removal program could cost more up-front, but a facility executive should also consider the indirect costs, like an overworked staff, when making a decision.
2. Take Advantage of Data
Companies tend to spend an average of 3% to 10% of their facilities’ budget on snow and ice removal, depending on their size and geographical footprint. However, taking advantage of historical data can also highlight what locations account for the biggest portion of the previous year’s snow removal costs, leading to better decisions when moving into the next season.
Many companies that internally collect data find out later that their data doesn’t provide an accurate and granular overview of last year’s snow season. Teaming up with a company that extensively tracks data and uses technology can provide a complete picture to make future decisions.
3. Make Small Changes to Affect the Big Picture
Small efforts in the right direction can reduce the total cost of ownership in facilities maintenance. By doing some research on the materials used throughout snow and ice season, a facility executive can opt out of using last year’s materials and replace them with more affordable alternatives.
For example, salt can vary in expense depending on the type. Sodium Chloride, Calcium Chloride and Magnesium Chloride are all options that vary in price. It’s also important to note that different types of salt also vary in performance at different temperatures.
4. Find The Most Compatible Cost Structure
By using historical data and making strategic decisions, facility executives should have an overarching idea of their facilities’ needs. Understanding materials’ costs and recognizing gaps in snow removal plans can help a facility executive identify the pricing strategies that are the most compatible with their facilities.
For example, if a facility executive has locations in different regions that experience varying weather conditions, they would benefit from using a seasonal variance pricing strategy. In this pricing strategy, facilities with locations across the country can allocate money from a location that received little snowfall for a location that incurs heavy snowfall.
What Can I Do to Make Sure I’m Satisfied with My Snow Removal Plan?
Make informed choices when building your snow removal plan by using trustworthy data. The more data you have to ground your decisions, the better chance you have of satisfactory outcomes for your bottom line and your customers.
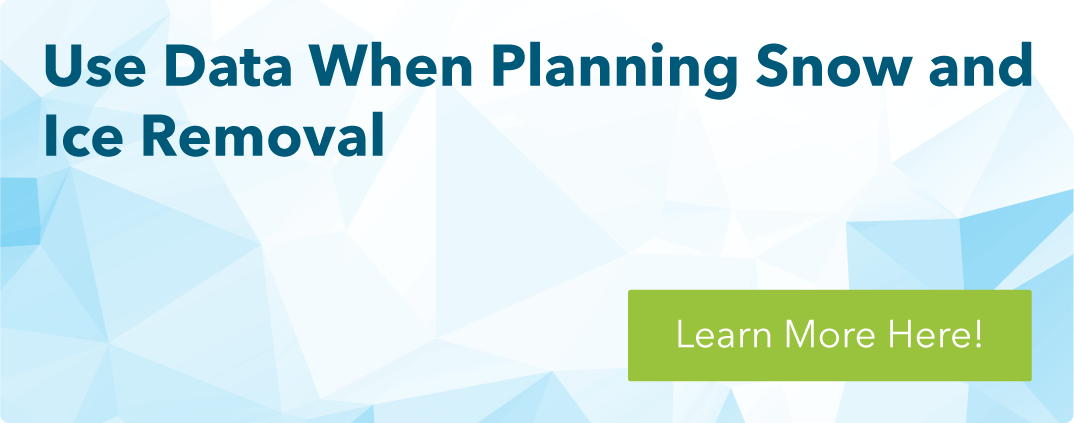
.avif)
- This is my list