4 ways preventative maintenance can stabilize budgets in logistics and warehouse facilities
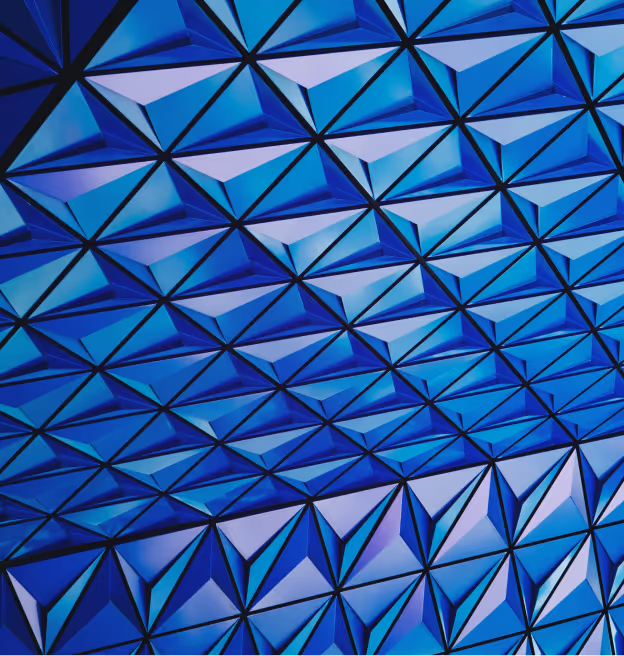
Facilities maintenance is a critical aspect of logistics and warehouse operations that is often overlooked. Warehouse facilities are the backbone of supply chain management, serving as hubs for storing, processing, and distributing goods. However, these facilities are subject to wear and tear, equipment breakdowns, safety hazards, and other issues that can disrupt operations and impact efficiency. This is where facilities maintenance plays a crucial role in ensuring smooth operations, preventing downtime, reducing costs, and maintaining a safe working environment.
Implementing a robust preventative maintenance program can ensure that logistics and warehouse operations meet critical uptime metrics while helping to stabilize overall facilities budgets. Over time, a good preventative maintenance program starts to reduce expensive critical repairs and reduces the need for deferred maintenance, allowing for greater capital expenditures to upgrade assets.
These are four ways that preventative maintenance can stabilize budgets and provide a good return on investment.
Less money spent on emergency repairs
Preventative maintenance, which involves scheduled inspections, routine servicing, and proactive repairs, can significantly reduce repair costs in logistics and warehouse facilities. Regular maintenance helps identify and address minor issues before they turn into major breakdowns, avoiding costly repairs or replacements. For example, conducting routine checks on material handling equipment, such as forklifts, conveyor systems, and automated machinery, can detect wear and tear, loose bolts, or faulty components that could cause expensive breakdowns if left unaddressed. By fixing these issues proactively, facilities can avoid unexpected repairs and associated downtime, leading to cost savings in the long run.
Lower operational costs
Effective preventative maintenance can lead to lower operational costs in logistics and warehouse facilities. Well-maintained equipment tends to operate more efficiently, consuming less energy and reducing operational costs. For instance, regular maintenance of HVAC systems can help optimize energy usage, ensuring proper temperature and humidity control, and preventing equipment strain or failures that could result in increased energy consumption. The U.S. Department of Energy recommends monthly HVAC maintenance to maximize efficiency and lower operating costs. A dirty filter adds stress to the air intake system and increases energy consumption, but preventative maintenance breaks the inefficient cycle, saves energy, and reduces costs.
Additionally, well-maintained facilities are less prone to safety incidents or accidents, which can result in costly legal liabilities, workers' compensation claims, and insurance premiums. By investing in preventative maintenance, facilities can mitigate such risks and minimize operational costs associated with accidents or incidents.
Extended equipment lifespan
Another significant benefit of preventative maintenance in logistics and warehouse facilities is the potential to extend the lifespan of equipment and assets. Warehouse facilities often house expensive and specialized equipment, such as conveyors, automated sorting systems, and storage racks, which are critical for smooth operations. Regular maintenance can prevent premature wear and tear, corrosion, and degradation of equipment, ensuring their optimal performance and extending their lifespan. This eliminates the need for premature replacements, which can be costly, and maximizes the return on investment (ROI) for these assets. By extending the lifespan of equipment through preventative maintenance, facilities can minimize capital expenditures on new equipment and achieve long-term cost savings.
Improved facility reliability
Facility reliability is crucial for logistics and warehouse operations, as any downtime or disruptions can impact the entire supply chain. Preventative maintenance plays a crucial role in ensuring facility reliability by identifying and addressing potential issues proactively. According to the Journal of Architectural Engineering, a failing, leaking roof compromises the whole building envelope. Preventative maintenance protects it.
For example, inspecting the facility's structural integrity, electrical systems, fire suppression systems, and other critical components can help detect any signs of wear, corrosion, or malfunction that could lead to facility failures or downtime. By addressing these issues before they escalate, preventative maintenance enhances facility reliability, reduces unplanned downtime, and ensures smooth operations. This, in turn, helps maintain customer satisfaction, prevents revenue losses due to disruptions, and safeguards the reputation of the facility as a reliable logistics partner.
Preventative maintenance provides a good return on investment (ROI) for logistics and warehouse facilities. It helps reduce repair costs, lower operational costs, extend equipment lifespan, and improve facility reliability. By implementing a comprehensive preventative maintenance program, logistics and warehouse facilities can optimize their operations, minimize downtime, and achieve cost savings in the long run.
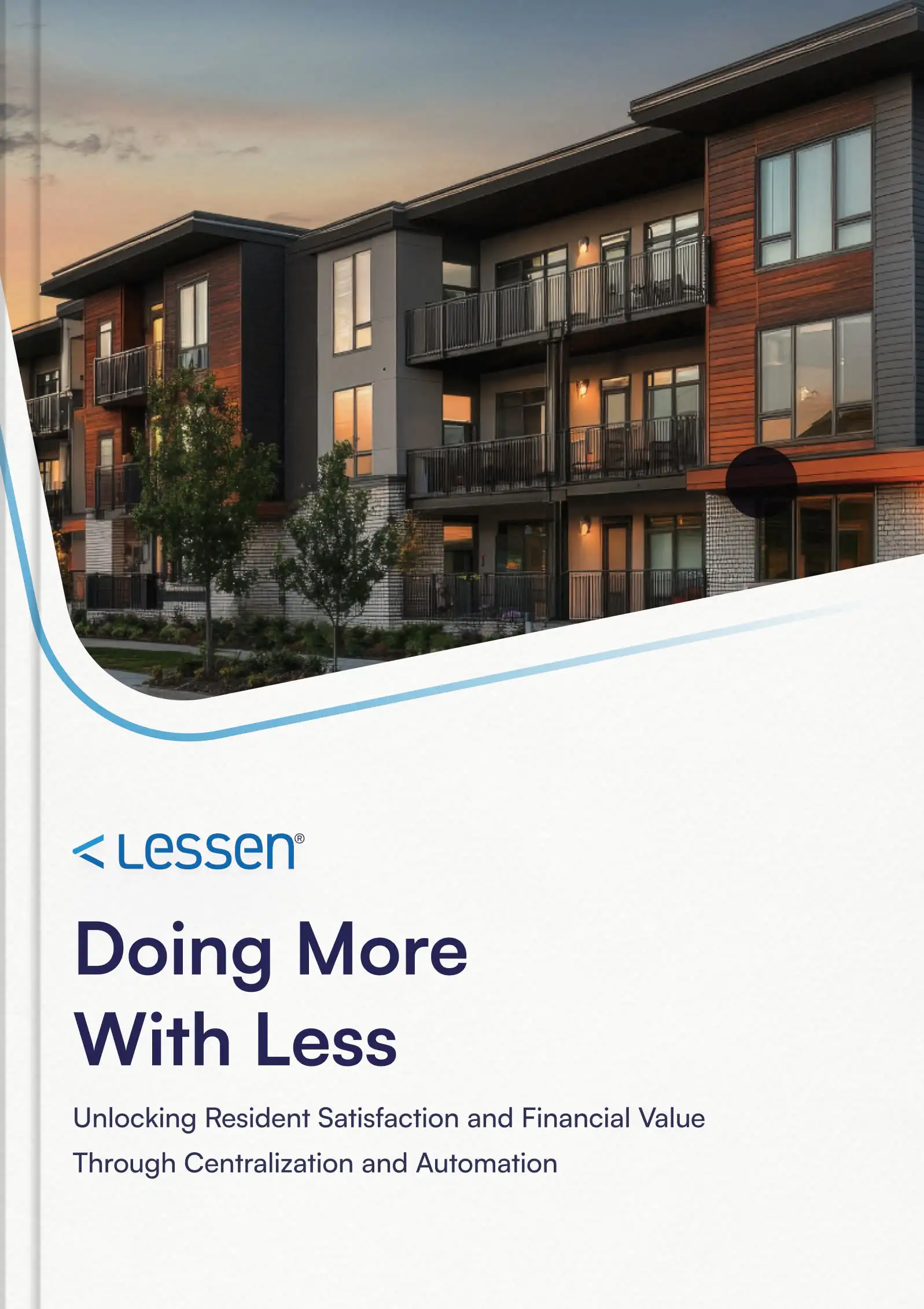
- This is my list