Facility Executive: Short on HVAC staff? Turn to tech
-min.avif)
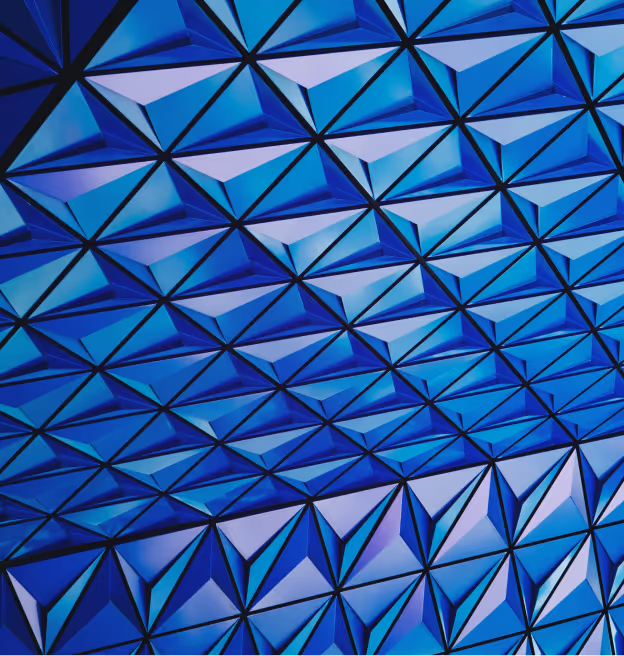
This article originally appeared on facilityexecutive.com.It’s becoming increasingly difficult to find (and afford) quality HVAC technicians, leaving facility executives coast to coast searching for solutions. One way to overcome the budgetary and logistical challenges presented by the “skills gap” affecting America’s skilled trades—caused by baby boomers retiring and a lack of interest among younger generations entering the workforce—is by harnessing today’s technology to promote preventive maintenance. Taking this approach is no less than a necessity given the industry’s workforce woes.The problem is so significant that the HVACR Workforce Development Foundation, whose mission is attracting committed and skilled employees to careers in the fields of HVAC and refrigeration, commissioned three studies in 2015 to examine the sector’s talent gap. “The core HVACR installation, maintenance, and repair occupations are among the most difficult to fill in the United States,” one of the surveys states. With the supply of HVAC workers shrinking, those in the field have demanded better benefits and higher pay. The annual mean wage for an HVAC mechanic or installer jumped nearly 22% (or from $39,710 to $48,320) between 2006 and 2016, according to the Bureau of Labor Statistics.These trends have created extra hurdles for facility executives, who are by the nature of their positions under constant pressure to keep costs in line. Fortunately, the latest technology puts preventive maintenance more closely within reach, allowing facility pros to mitigate—and even manage around—these challenges. Following are several types of capabilities offered by current technology for HVAC maintenance.Forecasting. Just as smartphone-powered weather apps with up-to-the-minute information are a lot more useful than relying on last night’s news, today’s facility forecasting tools are a leap beyond those of the past, providing an edge in a squeezed operating environment. An example from the rapidly expanding field of the Internet of Things (IoT)—in which devices share and act on real-time data— is an HVAC system control unit that can measure or “listen” to the sounds a fan makes, enabling predictions of when the equipment might fail and, in turn, triggering the ordering of preventive maintenance before costlier fixes are needed.Automated weather alerts can likewise sound the alarm on extreme conditions that might test HVAC systems, allowing for the strategic dispatching of technicians. This speeds up response times and makes the work order process more efficient, which is critical to overcoming the HVAC workforce shortage.Transparency. These forecasting tools are helpful on their own but, when combined into a centralized management platform capable of tracking thousands of data points and condensing those findings into a dashboard, these provide facility managers with a high level of transparency. Even a simple smartphone photo becomes something much more powerful in such a setup and goes a long way toward realizing preventive maintenance goals.Using a data-rich, cloud-based platform, managers can quickly view dozens of images of job sites and pieces of equipment from technicians out in the field, getting verification that scheduled work has been completed. Those images, when accompanied with warranty details, repair histories, and property records, are turned into asset records. Stored in a database, these records are transformed from disparate pieces of information into actionable insights.Work order avoidance. An even better outcome than more efficient repairs, of course, is avoiding some repairs altogether, and that too can be made easier with the use of technology tools. With asset readings and historic performance metrics, facility executives can better determine, for instance, whether all aspects of a site’s scheduled maintenance are necessary, freeing up focus and funds for components that show signs of wear.And when technicians have web-based tools like task-specific guides on their phones, even those who are less experienced can map out the best course of action when assigned a job, avoiding unnecessary work, repeat site visits, and wasted materials. In the case of a system-wide HVAC issue being caused by a single unit, these tools can work together to identify the culprit and suggest solutions, reducing the amount of time spent troubleshooting, and figuring out how to proceed.For one national retailer using a cloud-based management platform, the implementation of a seasonal preventive maintenance plan based on live data from its HVAC systems led to double digit decreases in work order response and resolution times. This helped to trim the maintenance spend by up to 20% per store. That’s a real difference. And given the workforce issues adding pressure to what’s always been a challenging role, it’s a difference today’s facility executives can’t afford to ignore.
-min.avif)
- This is my list