Confronting HVAC Costs is Worth the Wager
-min.avif)
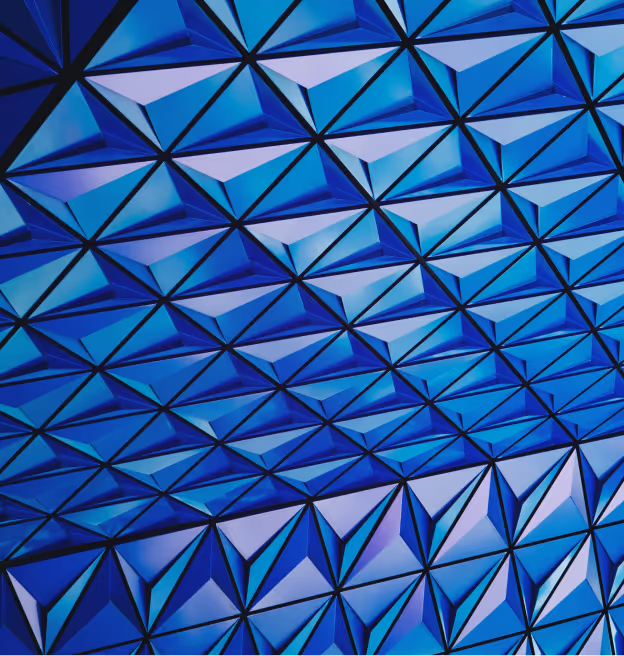
Everyone knows HVAC expenses can be challenging to measure and manage. Understanding your true costs for service and repairs, installations, and energy can improve your ability to manage the long-term total cost of ownership. Confronting these financials will help organizations develop and manage a budget objectively. Below are some common cost components of an HVAC system and the strategies to optimally measure and manage them.
1. Service and Repair Costs
Service and repair costs made to an HVAC system include both direct and indirect costs.
In most cases, organizations typically measure direct costs such as hourly labor from in-house or third-party technicians, parts, materials and travel charges to determine the lowest total service cost. However, many focus on hourly labor rates, which is just one variable in a much larger equation.
For example, a highly skilled HVAC technician may cost $100 per hour but can complete the work of a less experienced HVAC technician with a lower hourly rate in half of the time. Additionally, a technician that provides higher quality services will result in fewer return visits, which will ultimately reduce the total cost of a work order.
Again, direct cost analysis only provides half of the view into the complexities of the total service cost.
Total service cost analysis requires quantifying direct and indirect costs. Indirect expenses include, but are not limited to, a call center, invoice processing, asset tracking, landlord responsibility, warranty management, sourcing and vendor management, potential lost sales, weakened brand experience, CMMS development and maintenance, analytics and reporting and more.
Together, direct and indirect costs equate to the true total service cost. By not including indirect costs or all variables, managers fail to promote financial transparency and the efficient use of resources.
2. Installed Costs
Installed costs include all the necessary equipment and labor for the installation of a new HVAC unit. Some of the expenses consist of factory-installed options, field-installed accessories, controls, air distribution systems and commissioning.
Typically, the installation costs of a new HVAC unit can be 10-20% higher when it is on an emergency or reactive basis. Furthermore, property managers dealing with this crisis are more likely to bypass the cost aspect of the equipment because they are interested in remediating the situation as quickly as possible. That can be costly. However, it is possible to include these costs in a budget by taking a proactive approach to installing new units.
A unit replacement program allows companies to identify aging and inefficient HVAC units proactively through past data and move forward with a replacement. This data includes but is not limited to asset age, performance history, usage, maintenance, manufacturer, location and past maintenance calls.
By taking this proactive option, companies can receive access to high-efficiency equipment, target the stores that need new assets and potentially see a 10-20% cost difference over a typical project. Eliminating the stress that comes from installing a unit in the middle of the summer is also a benefit of being proactive.
3. Energy Costs
Energy costs consist of the electricity and natural gas needed for cooling, ventilation and heating. While these costs vary by the geographic location of each store, there are a few easy methods to minimize the costs associated with an inefficient and overloaded HVAC system:
- Replacing filters and cleaning coils on a consistent basis ensures a unit is running as efficiently as possible.
- Using an Energy Management System (EMS) to control asset use and gain insight helps decrease energy and service costs.
An EMS system controls, monitors, and analyzes all HVAC systems remotely so a company can set temperature controls to reduce usage during peak demand hours to hit their target budgetary spend.
Integrating an EMS with a facilities maintenance program can help HVAC units operate more efficiently and consume less energy, which reduces overall costs and extends assets' lifecycles in the end.
Using these best practices can help companies better understand the true life cycle cost of their HVAC systems and programs. With this objective data, organizations like yours will utilize the best information when making program decisions. Partnering with a facilities maintenance company can also provide organized asset information, reliable and beneficial relationships, and technology that offers clarity into your program.
-min.avif)
- This is my list