Here we go again: Supply chain issues, staff shortages, and rising costs continue to impact facilities maintenance
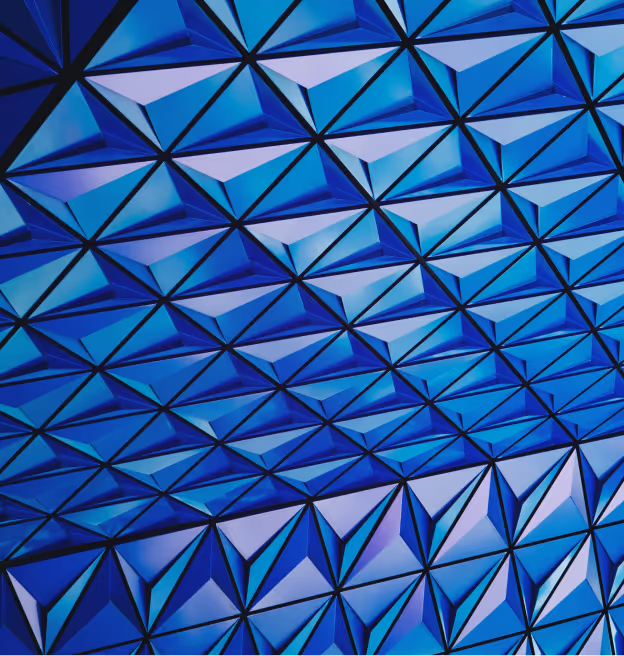
Staffing shortages, supply chain delays, and inflation continue to increase operational and facilities costs. Even though their roots started early on in the pandemic, they have compounded over time to create challenges that are not easily addressed with routine solutions.
Facilities managers and store operators are currently caught in a dilemma: the need to fight higher costs because of inflation yet the need to hire more workers to meet increasing demand at higher wages. This has been most acute for companies with multiple locations and has hit everything from critical assets such as HVAC to routine maintenance like landscaping. These wage and supply chain pressures put added strain on monthly budgets. For facilities and store managers, this could lead to difficult choices on maintenance and equipment upgrades.
Companies looking to whether the near term will often defer maintenance requests until future budgets can provide some flexibility. However, this scenario usually never arrives. Companies looking to preserve existing capital while not leveraging future budgets are increasingly turning to tech-enabled approaches where reactive maintenance needs are outsourced and centralized while budgets build for future asset requirements. We take a closer look at the three areas exerting the most pressure on facilities and strategies to address them.
Staffing Shortages
The lack of available workers continues to be a primary challenge that store operators and facilities managers face. In an industry where higher turnover is the norm, the pandemic has only deteriorated the situation over the past few years. These staff shortages have made it more difficult to meet new demand or routine business needs. This presents two unique challenges for facilities operators and especially those with distributed portfolios: 1) not enough staff to perform routine cleaning duties; and 2) not enough service providers available to repair or maintain equipment.
Prevailing Labor Shortage Issues
When it comes to finding skilled workers to service equipment, the prevailing challenge is low number of technicians entering the field to replace a retiring workforce. With the training and licensing for these fields taking potentially years to achieve, fewer technicians are being trained each year and the number of new technicians entering the field isn't enough to keep up with those leaving. The aging demographics of trade workers combined with the average older entry age of new skilled workers are contributing to the problem and ensuring that the concerning labor shortage continues.
As these issues continue, equipment such as HVAC, lighting, plumbing, electricity, floors, doors, and structural components continues to age and goes without routine maintenance, compounding issues over time. Because of parts shortages and labor delays, it's taking even longer to resolve these issues, which means that they are likely to grow and become bigger maintenance problems over time.
Consequently, as staffing shortages persist, there has been a surge in demand for facilities management, partly because of the need for extra cleaning and sanitization services at commercial sites, but also because of the reluctance of managers to task staff with routine cleaning duties. This has allowed companies to preempt spikes and drops in demand through data insights that can anticipate the providers needed for specific projects.
Possible Solutions to Manage Staff Shortages
Regardless of the issues facing facilities and store managers as a result of labor shortages, there are solutions available to better manage the situation.
The most obvious solution is using available technology to help ease the pressures brought on by this particular challenge. Simple technology and software can streamline processes and remove manual steps from workflows. More advanced and sophisticated tools and platforms can help balance workloads, organize and track work orders, and allow for the proper allocation of limited labor resources. This ensures that the workforce that is available is being assigned to only the most relevant work orders so that no labor resources get wasted.
With the right tools, available technicians can be proactive rather than reactive; they are able to address issues earlier or provide routine maintenance to avoid major issues that take extra time and money to resolve. Although this doesn't directly solve the staff shortage problem, it does ensure that available labor resources get used more effectively which could possibly help avoid extended backlogs.
Supply Chain Shortages and Delays
Another critical area affecting companies when it comes to facilities maintenance is supply chain shortages and delays. Exacerbated as a result of the COVID-19 pandemic, there has been a consistent shortage of tools, equipment, and other supplies required for facilities maintenance, which has caused the prices of some HVAC equipment to increase by 80 percent.
Prevailing Supply Chain Issues
Supply chain disruptions have been going on for over two years. Unfortunately, it seems that supply chain shortages and product delays are here to stay for a while. This, of course, has had a significant impact on facilities and operators.
The principal issues is the inability of service providers to find product. Even though supply chain issues have eased for some products, it has not been equal, especially in larger assets like rooftop HVAC units. This causes work orders to be delayed while pending work orders are backlogged. Technicians routinely are unable to procure the necessary parts to fix equipment or just don't have the resources to do routine preventative maintenance.
A lack of supplies also means a lack of growth opportunities for businesses, which are now faced with stagnating workloads, loss of labor forces, and a lack of growth. In many cases, this is also contributing to an erosion of capacity. Businesses rely on facilities maintenance for numerous services, and a lack of these routine tasks affects their overall functioning. Subsequently, this challenge feeds into another huge challenge the industry faces: rising costs.
Potential Solutions to Supply Chain Shortages & Delays
The pandemic wasn't solely responsible for the current supply chain issues, but it played a part. Underlying economic issues such as economic changes, logistics best practices, and fluctuating exchange rates were affecting the supply chain already, and the pandemic only served to expose these weaknesses across all industries sooner.
One of the simplest solutions to this problem for businesses is to form mutually beneficial partnerships that serve to strengthen their supply chain. For example, companies should find partners with the right connections and tools that can support them when it comes to facilities maintenance requirements, both planned and unplanned. Best-in-class providers can navigate the challenging supply chain environment and focus on solving these types of challenges, removing the stressors on the business and offering the potential for a more powerful and long-term solution. Connecting to multiple sources can help companies avoid the pitfalls of only having a single supplier.
Another solution is using technology, like mobile apps, to organize calendars and streamline communication on supply matters. By making the process as efficient as possible while providing visibility and transparency regarding any possible hurdles, unexpected supply chain delays or shortages can be mitigated. An integrated facilities management system is designed to organize and streamline every part of the process so only providers that have access to the necessary supplies are assigned to work orders.
The Rising Costs of Facilities Maintenance
Continued labor and supply chain shortages have resulted in upward pressure on price. Notably, the highest costs for both labor and materials are associated with HVAC, janitorial, plumbing, and electrical services. This upward trend in facilities management spending is predicted to continue.
Prevailing Rising Costs Issues
Although the previous challenges addressed have caused costs to increase for the facilities management industry, inflation has also contributed to the overarching problem and is starting to weigh down facilities maintenance decisions.
The swift increase in materials costs makes operations more expensive across the board. Business are faced with absorbing these costs, eating into margin, or passing them along to customers, eating into sales. The rising costs due to inflation are now on par with supply chain disruptions as the biggest blow to the industry in the wake of the pandemic.
Possible Solutions to Rising Cost Challenges
Just as with the other hardships facing facilities management, there are some potential solutions. Partnering with a company that has subject matter experts on critical equipment can provide insight into which assets need to be repaired or replaced and on what schedule. Even though supply chain and labor issues are out of direct control, having better insights through advanced data will lead to better decisions on where to allocate budget. By doing this and smartly delaying costs while still addressing maintenance, companies can wait for falling prices, protect future budgets, and still address current needs.
Streamline and Automate Your Facilities Management
Facilities maintenance continues to face unprecedented challenges. Focusing on what can be controlled, such as which providers to contract and which assets to service, can provide some relief and planning. However, this can be extremely time-consuming. Partnering with a provider can streamline and automate your facilities management processes while also navigating the various challenges in the field on your behalf.
About SMS Assist
At SMS Assist, we facilitate high-volume contracts with our extensive network of service providers, which enables us to secure the best available rates for our customers. We aim to match your facilities management needs with the best vendors who have adequate staffing and access to the necessary supplies while negotiating reasonable rates. By partnering with us, you not only save time and money but also valuable resources.
Our cloud-based platform connects every part of your facilities management in one convenient platform and manages the end-to-end work order process to make your life easier. Additionally, we use our contacts to better empower service providers in our network with the technology and resources they need so that they can better serve your business. Finally, your business is managed by a dedicated team that oversees every aspect of your facilities' maintenance requirements, from preventative maintenance to reactive maintenance and everything in between. Request a demo from SMS Assist today and discover how we can help you overcome the challenges you face.
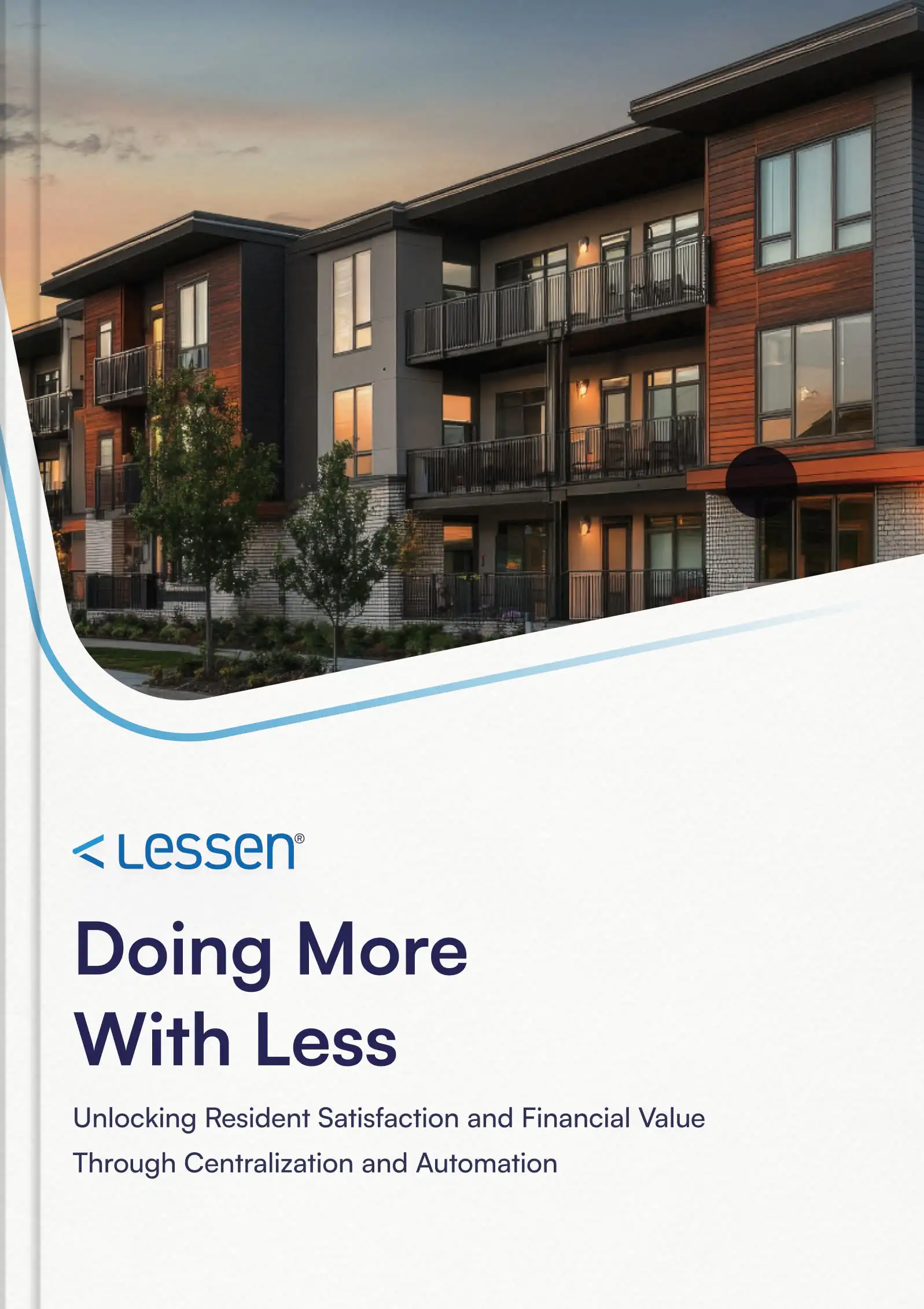
- This is my list