5 ways a reactive HVAC replacement plan is hurting your budget
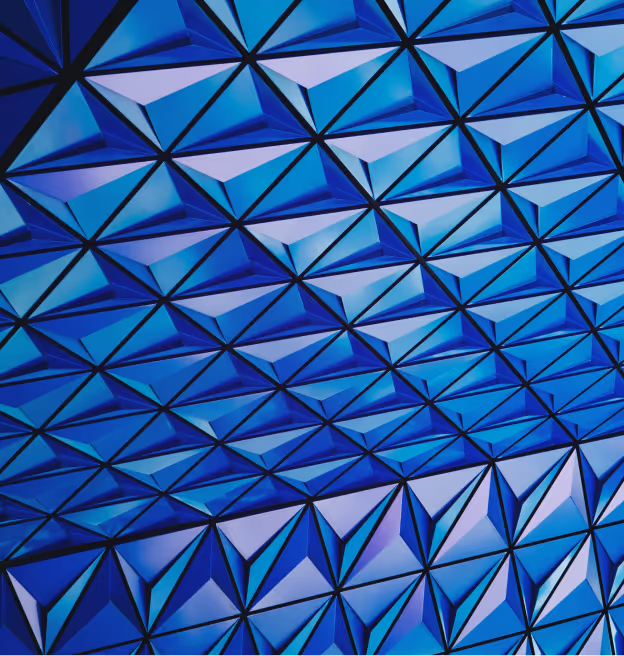
Any retailer knows that in-store temperature matters a great deal to customers due to its affect on their overall shopping experience. Imagine trying on new clothes while perspiring in your dressing room or browsing a store while shivering. Retailers are privy to the fact that most heating, ventilation, air conditioning (HVAC) equipment breaks down at the worst imaginable times. Situations like these are caused when the equipment’s performance is stretched to its limits during extreme heat or cold and your asset falls short.
So, why are so many retailers so reactionary to this critical maintenance category?
Reactive maintenance isn’t without advantages...at least on paper. Otherwise, it wouldn’t be such a challenging approach to overcome. Unfortunately, the money saved by delaying HVAC replacement tends to grow until it’s a looming expense when replacement reaches mission-critical. According to Avonda Air Systems, unplanned service calls cost as much as 9 percent more than planned maintenance. They explain, "As you’re forming your plan, consider this: reactive maintenance should only be performed on components that are inexpensive, easy to replace, where failure does not cause collateral damage in the system."
Here are some of the ways reactive HVAC replacement strategy can cost your stores:
1. Higher equipment pricing
Proactive replacement gives retailers the ability to specify and bid out equipment from several equipment manufacturers, which will help control equipment cost and related replacement parts. Even though this only amounts to 10-15% of a typical equipment lifecycle cost (with maintenance and energy expense evenly sharing the remaining lifecycle costs), sufficient availability of equipment and parts are often more important than their cost.
2. No consolidation of resources
Several components associated with the installation can be optimized during a planned HVAC replacement. Crane rentals, equipment transportation, travel charges, recycling opportunities, etc. are necessary whether replacing just one or all rooftop units (RTUs). These costs, when consolidated into one or multiple total replacements in a specific geographic area, can significantly reduce cost when compared to that incurred for a single unit replacement.
3. Inability to redesign
By accounting for changes made since the store’s original design, including receiving feedback from store personnel or even customers, it affords the opportunity to improve comfort delivery by reducing equipment and capacity while improving energy efficiency, which helps reduce energy expense. This may even include “future-proofing” by adding technology such as Energy Management Systems (EMS) or other control technology
4. No utility rebates or taxes
Pursuing utility rebates, tax or other incentives can help offset the cost of the overall project, but may also require some planning. Many utility companies provide energy rebates for replacing old equipment with more energy-efficient equipment and will help improve the return on investment of the HVAC replacement project. Usually, utility companies require an assessment or analysis prior to the replacement in order to qualify for a rebate, which would be virtually impossible during an emergency replacement.
5. No way to stagger the project
Most retailers have grown their store footprint over time, which affords them the ability to cluster stores of similar age and geography. Most HVAC RTU’s last between 13 and 15 years, so projects can be rolled out to stores that are of similar age. The project can then further be prioritized based on electric and gas utility rates, temperature extremity, and utility rebate availability. Emergency replacements don’t have this luxury.
HVAC maintenance usually ranks at the top of retailers’ budgets, but despite their best efforts to perform preventative maintenance to help control cost, an unusually hot summer or cold winter can easily impact a company’s bottom line. Still, a proactive approach to HVAC replacement enables timely planning, which avoids many of the unknown issues, and could avoid catastrophic failures that could potentially lead to store closures. Planned replacement affords you the luxury of maintaining control over store comfort while managing overall cost.
To learn more about managing FM costs, check out our whitepaper: How to Calculate the True Cost of Facilities Maintenance.
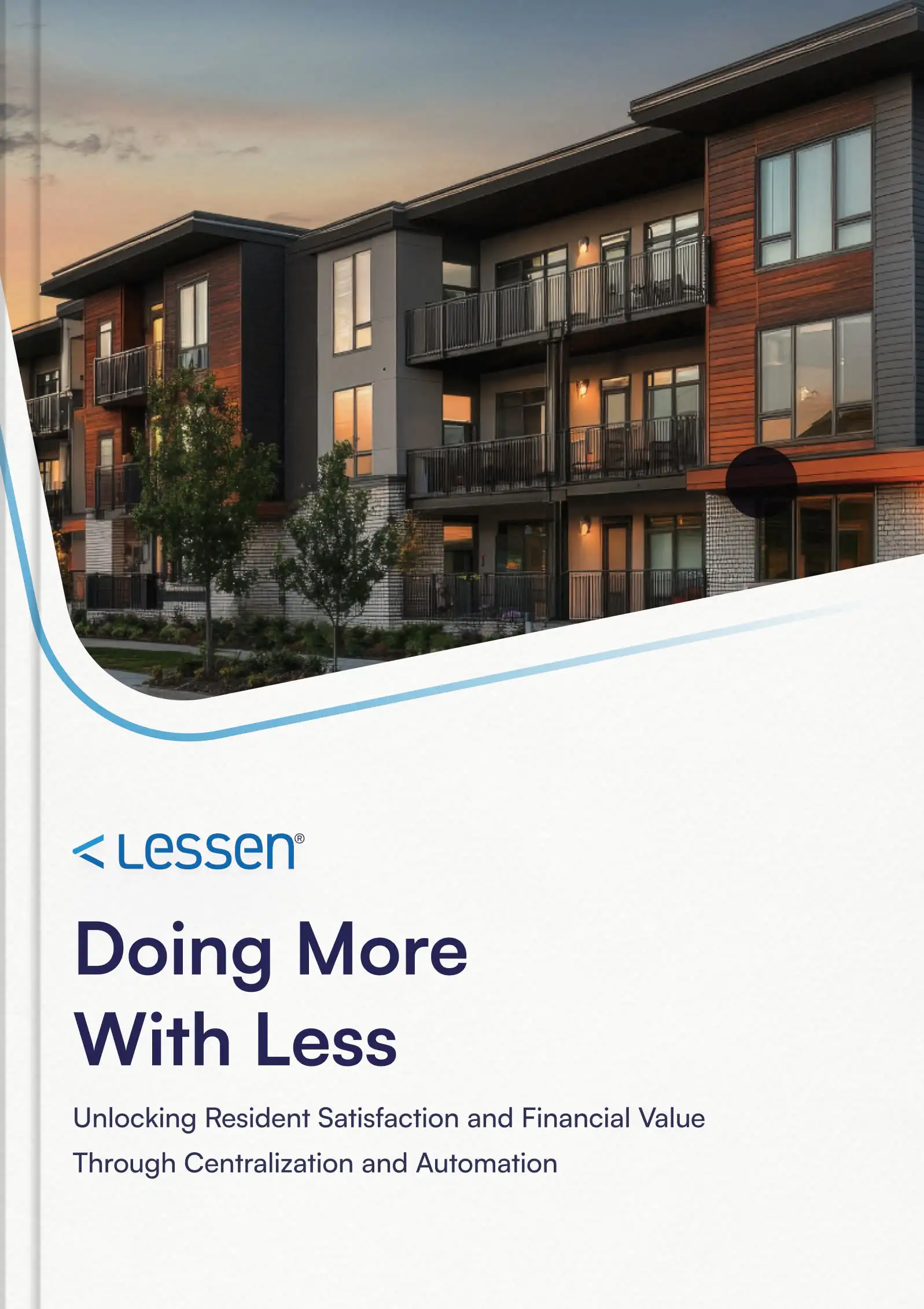
- This is my list